Avoneer
|
posted on 19/7/05 at 11:01 AM |
|
|
Soldered nipples (ooo err) for cables
Anyone anby experience with soldered nipples on the ends of cables such as the handbrake, accelerator and clutch?
Pat...
No trees were killed in the sending of this message.
However a large number of electrons were terribly inconvenienced.
|
|
|
scoobyis2cool
|
posted on 19/7/05 at 11:10 AM |
|
|
If you're wondering about their strength, I'm sure I read once that someone had tested their soldered nipple and had managed to snap the
cable before the nipple gave way, so they're easily strong enough!
Pete
It's not that I'm lazy, it's that I just don't care...
|
|
Mix
|
posted on 19/7/05 at 11:18 AM |
|
|
Make sure you 'fan out' the individual strands so as they ffill the recess in the nipple, dress back with a file once soldered, and all
the usual cleanliness comments.
Definitly less prone to failure if made correctly than the screw type.
Mick
|
|
NS Dev
|
posted on 19/7/05 at 11:56 AM |
|
|
yep, used em a few times, no probs, but as Mix said, make treble sure that everything is spotlessly clean first. (wash in acetone or similar)
|
|
rusty nuts
|
posted on 19/7/05 at 05:42 PM |
|
|
If you need to cut the inner cable don't use pliers sidecutters etc . A tip I was shown years ago is to use a sharp chisel, place the cable onto
a hard surface such as a vice , place chisel across point to be cut and give the chisel a smart tap with a hammer , clean cuts everytime with no
fraying. HTH .
|
|
907
|
posted on 19/7/05 at 07:54 PM |
|
|
quote: Originally posted by scoobyis2cool
If you're wondering about their strength, I'm sure I read once that someone had tested their soldered nipple and had managed to snap the
cable before the nipple gave way, so they're easily strong enough!
Pete
Hi. Was this it ?
I should point out it is silver solder, not soft solder.
The crimping tool was a £3.49 set of bolt cutters with a round notch filed in the jaws.
(For £3.49 you don't get hard jaws.)
HTH Paul G
 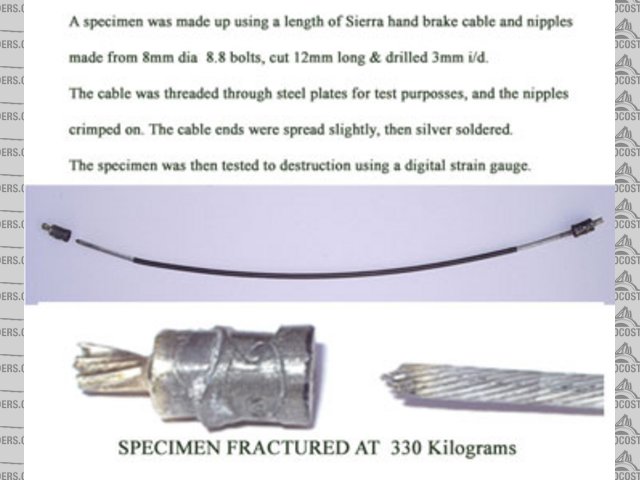 Rescued attachment Lotus 003.jpg
|
|
scoobyis2cool
|
posted on 19/7/05 at 08:13 PM |
|
|
That might have been it, it was a long time ago so I can't remember for sure. Either way I think it shows there aren't any strength
issues!
Pete
It's not that I'm lazy, it's that I just don't care...
|
|
Avoneer
|
posted on 19/7/05 at 09:57 PM |
|
|
Any pics of the bolt croppers?
I pressume you can also do it with a smaller bolt and it still be strong enough?
Cheers,
Pat...
No trees were killed in the sending of this message.
However a large number of electrons were terribly inconvenienced.
|
|
Rorty
|
posted on 20/7/05 at 04:52 AM |
|
|
Some solder will inevitably wick its way along the cable for a short distance and this is where the cable will break..right where the solder ends.
The cable's strength will have been lost due to being over heated and it is at its weakest right where the solder ends.
It's not a difficult thing to do, but if your cables keep breaking just short of the nipples, you know you're burning the cable. If the
cable gets more than dull red, you've destroyed it. Use a low flame and heat it gently then when the nipple and cable are the same shade of dull
red, then touch the solder onto the end of the cable until it almost fills the reservoir in the nipple. If it's done cleanly and slowly,
there's no need to splay out the ends of the cable.
Finally, don't disturb the cable/nipple until it's stone cold and then rinse it under the hot tap to remove the hardened (and corrosive)
flux.
Cheers, Rorty.
"Faster than a speeding Pullet".
PLEASE DON'T U2U ME IF YOU WANT A QUICK RESPONSE. TRY EMAILING ME INSTEAD!
|
|
907
|
posted on 20/7/05 at 05:34 PM |
|
|
quote: Originally posted by Avoneer
Any pics of the bolt croppers?
I pressume you can also do it with a smaller bolt and it still be strong enough?
Cheers,
Pat...
Hi Pat,
Pic as requested.
And size dosn't matter
Mine were 8 mm to match the 8 mm cable adjusters that the nipples pull against.
hth
Paul G
  Rescued attachment bolt-cropper-s.jpg
|
|
Monkey Man
|
posted on 9/8/05 at 09:14 AM |
|
|
Hi. Was this it ?
I should point out it is silver solder, not soft solder.
HTH Paul G
Hi, I'm resurrecting this because I need to put an end on my handbrake cable and got pointed at this thread yesterday. I've done a few
searches for silver solder and the stuff I get back claims to have a lower melting point than ordinary electrical solder and be ideal for
microelectronics. Which doesn't sound like what you're talking about. How di I know what the right stuff is?
Thanks,
|
|
britishtrident
|
posted on 9/8/05 at 09:20 AM |
|
|
Look in a B&Q Wharehouse in the plumbing section --- I think Halfords might also do among the welding accessories.
Re cutting cables before threading through the nipple solder the cable leaving a bit extra first then cut at the soldered section. Then thread
through the nipple and cut the soldered bit off and fan out the ends and solder to the nipple.
|
|
Mix
|
posted on 9/8/05 at 09:24 AM |
|
|
Try searching for info under 'hard soldering'
I use 'Easyflow' grade and flux
Mick
|
|
Monkey Man
|
posted on 9/8/05 at 09:34 AM |
|
|
Thankyou both.
|
|
chrisf
|
posted on 9/8/05 at 12:53 PM |
|
|
I may be doing this soon as well. When you guys discuss the solder, are you talking about a standard electronics wiring solder gun and wiring solder?
Or are you talking about a butane torch with non electrical solder?
--Thanks, Chris
|
|
David Jenkins
|
posted on 9/8/05 at 12:58 PM |
|
|
I'm surprised that easyflo silver solder is recommended - I've often used this in model engineering, and it usually requires the piece to
be taken to a dull orange before it will start to flow (and easyflo is one of the lowest-temperature silver solders). I would have thought that this
temp would have wrecked the properties of the cable.
I would have thought that a very hard tin-lead solder such as Comsol* would be more appropriate (* if you can still get it!).
David
|
|
paulf
|
posted on 10/8/05 at 10:24 AM |
|
|
When I shortened the handbrake cable on my car i threaded it through the nipple spread the ends and welded it with the mig. I was unsure about
silversoldering it due to the heat on ther cable but have had no problems this way, I think soft solder would pull through after a while.
paul.
|
|
britishtrident
|
posted on 10/8/05 at 12:18 PM |
|
|
MIG works surprisingly well on handbrake cable :-)
|
|
geoff shep
|
posted on 10/8/05 at 01:52 PM |
|
|
You can introduce a bit of solder - not too warm - to the area you want to cut, then you can use ordinary wire cutters and it will cut cleanly without
fraying.
For the nippling(!) I used the RH method, which I thought a bit suspect at the time, of drilling hole lengthways through a piece of bolt, threading
the cable through a then giving it a welt with a big hammer. Its still holding firm 10 years later.
|
|
britishtrident
|
posted on 10/8/05 at 02:20 PM |
|
|
For silver soldering I use a little oxy-propane torch and pre-flux rods
|
|
miserableoldgit
|
posted on 11/8/05 at 10:27 PM |
|
|
An old motorcycling trick my old-man showed me once was to tap a small Cobblers Tack into the end of the cable to spay it out, then solder it in.
Acts a bit like the wedge in the top a a hammer stale.
Youth and vitality are wasted on the young
|
|