aitch
|
posted on 3/12/09 at 02:54 PM |
|
|
BEC composite chassis early stages
as the title says im in the very early stages (still thinking really) but after reading the composite chassis thread in chassis section believe it
would be possible to make a LOCOST composit type mid engined BEC
rather than posting the details of chassis constructin here ill add a link to the other thread
http://locostbuilders.co.uk/viewthread.php?tid=123349
just wondered what peoples thoughts were as an idea
i will be posting on here quite a bit asking some very daft questions so please bear with me.. the things im most unsure of at the moment are chain
driven diff and how to make it reverse, i know there are commercially available diffs that will overcome both of these issues, however i am looking
for LOWCOST options on everything
aitch
[Edited on 3/12/09 by aitch]
[Edited on 3/12/09 by aitch]
 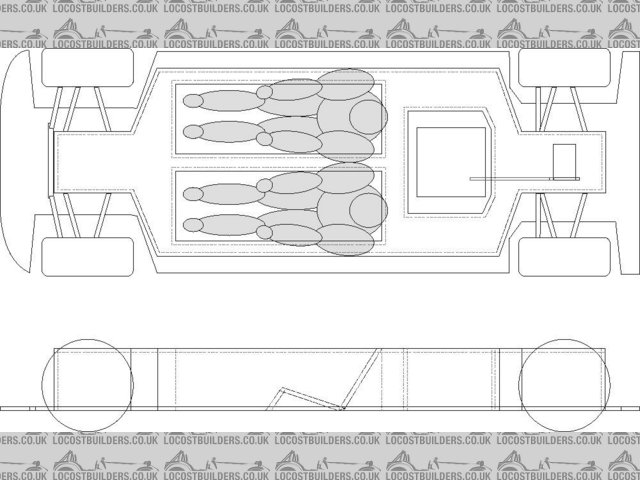 Rescued attachment Kit Car.JPG
|
|
|
belgian2b
|
posted on 3/12/09 at 03:08 PM |
|
|
Hello,
when i was a student, i worked for some month with Gillet in Belgium which is the builder of the Vertigo.
This car has a carbon fiber chassis.
The chassis is build like a bath tub, with , at the front , inbord suspension.
The chassis ends , at the rear just behind the driver seat.
A steel frame support the differential and rear suspension.
That chassis has no edges ( corner between under part and vertical sides).
In fact, edges are rounded
It seems that this give more strenth to the chassis.
So from what i know, may be you should try to make you desing more simple and more "soft on edges".
Nice idea you have,
Gerardo
|
|
aitch
|
posted on 3/12/09 at 03:57 PM |
|
|
quote: Originally posted by belgian2b
Hello,
when i was a student, i worked for some month with Gillet in Belgium which is the builder of the Vertigo.
This car has a carbon fiber chassis.
The chassis is build like a bath tub, with , at the front , inbord suspension.
The chassis ends , at the rear just behind the driver seat.
A steel frame support the differential and rear suspension.
That chassis has no edges ( corner between under part and vertical sides).
In fact, edges are rounded
It seems that this give more strenth to the chassis.
So from what i know, may be you should try to make you desing more simple and more "soft on edges".
Nice idea you have,
Gerardo
Thanks Gerado
the design enables using flat sheets to make construction simple and cheap (ish) and uses box sections to acheive stength. its not the most elegant or
strongest solution by any means, and the construction technique is questionable anyway without a lot of structural analysis, but its just an idea as
an alternative to steel space frame, i will look into it more (a lot more) before making any decisions, the only thing im sure of at this stage is mid
engined BEC..
aitch
[Edited on 3/12/09 by aitch]
[Edited on 3/12/09 by aitch]
|
|
kendo
|
posted on 3/12/09 at 08:19 PM |
|
|
"Composite Chassis"
Generally the aim of making a composite chassis, as per F1, F3, LeMans prototypes etc., is to get get significant strength without the weight penalty
of a fabricated metallic chassis.
To be frank, and here speaks the voice of experience (I was responsible for car in my avatar), that just isn't possible in a
"lowcost" fashion.
The industry has moved on and costs are coming down due to new techniques but thats cutting edge stuff and probably beyond the budget and capability
of 99% of diyers.
I don't want to pee on your bonfire, but there is possibly a practical way for you to achieve your goal.
You could use sandwich panels folded and bonded. Now they come in all shapes and sizes. A practical method is with ali skinned honeycomb from the
likes of Technical Resin Bonders in Huntingdon Cambs.
If you are handy with cad you could draw up all the bits you need and have them cut leaving you a 3d jigsaw to bond together with cleats.
Don't forget you are going to have to include bulkhead panels in your design to maintain strength.
|
|
aitch
|
posted on 3/12/09 at 10:07 PM |
|
|
quote: Originally posted by kendo
Generally the aim of making a composite chassis, as per F1, F3, LeMans prototypes etc., is to get get significant strength without the weight penalty
of a fabricated metallic chassis.
To be frank, and here speaks the voice of experience (I was responsible for car in my avatar), that just isn't possible in a
"lowcost" fashion.
The industry has moved on and costs are coming down due to new techniques but thats cutting edge stuff and probably beyond the budget and capability
of 99% of diyers.
I don't want to pee on your bonfire, but there is possibly a practical way for you to achieve your goal.
You could use sandwich panels folded and bonded. Now they come in all shapes and sizes. A practical method is with ali skinned honeycomb from the
likes of Technical Resin Bonders in Huntingdon Cambs.
If you are handy with cad you could draw up all the bits you need and have them cut leaving you a 3d jigsaw to bond together with cleats.
Don't forget you are going to have to include bulkhead panels in your design to maintain strength.
thats pretty much the design principle in the sketch all enclosed box sections made from bent from flat and or bent GRP-HONEYCOMBE-GRP
i know i need to do a lot more work and investigation.
aitch
|
|
Regsmonster
|
posted on 4/12/09 at 07:42 AM |
|
|
As you're in Nottingham.
My wife used to work (in the factory) for www.epmtechnology.com they are in Draycott. Might be useful for
future reference.
[Edited on 4/12/09 by Regsmonster]
[Edited on 4/12/09 by Regsmonster]
|
|
mr henderson
|
posted on 4/12/09 at 07:55 AM |
|
|
I've been fascinated by this subject for years, though the composite material I would want to use is birch plywood!. Anyway, what I have always
found is that the main difficulty is connecting the suspension subframes to the body tub, and in the end this is what has prveneted me from taking the
idea further.
It's a shame, because when you look at the middle part of a 7, it is absoultely ideal for fabricating from flat sheets of (whatever) material.
|
|
aitch
|
posted on 4/12/09 at 10:14 AM |
|
|
thanks
quote: Originally posted by Regsmonster
As you're in Nottingham.
My wife used to work (in the factory) for www.epmtechnology.com they are in Draycott. Might be useful for
future reference.
[Edited on 4/12/09 by Regsmonster]
[Edited on 4/12/09 by Regsmonster]
just had a quick look around the website and saved infavourites for future reference
aitch
|
|