ecosse
|
posted on 20/12/05 at 08:48 PM |
|
|
Chassis fab - 1 piece or sections?
Hi all
First post so be gentle
First time builder, I'm using the Mcsorley plans and have setup my jig, got the steel and getting ready to start cutting and welding.
Got a question before I start though (surprise!), the main chassis frames (front to back) are made up of 3 seperate cut sections of tube(A1/2, D1/2,
f1/2 & N1/2, J1/2 on the top rail), is there a reason why this is not done in single lengths, notched and bent to form the necessary angles,
instead of 3 butt welded sections?
Would that not be stronger than butt welding them together?
I tried a search but couldn't find any mention of this, have I lost the plot completely or is there a reason why not to do it this way?
All help/insight/abuse welcome
|
|
|
tks
|
posted on 20/12/05 at 09:07 PM |
|
|
i think
the trick is that
"every one" has an welder and an cutter at home but maybe not every one has bending fasitilities....
from some sentence i also say it would be better but on the other side bending means thinner wall and maybe then you create an weak point?
Tks
The above comments are always meant to be from the above persons perspective.
|
|
MikeRJ
|
posted on 20/12/05 at 09:22 PM |
|
|
I guess you mean cutting a 'V' out, bending and then welding the three cut sides? The strength won't be significantly different to
a (properly) welded butt joint, but a possible issue it that of distortion. Because you are only welding 3 sides, you may find the angle
"closes up" after welding. With 4 sides and carefull welding this can be minimised.
I don't think I've ever read of a chassis failure in these locations, so I would say that the book method is a sufficiently strong design.
|
|
Triton
|
posted on 20/12/05 at 09:34 PM |
|
|
Cut n shut is stronger than bending or cutting a "v"
My Daughter has taken over production of the damn fine Triton race seats and her contact email is emmatrs@live.co.uk.
www.tritonraceseats.com
www.hairyhedgehog.com
|
|
ecosse
|
posted on 20/12/05 at 09:45 PM |
|
|
Cutting a "v" was what I meant, thanks.
Cut n shut it is then, I should probably have figured that if the "V" Method was best it would have been done and documented by now!
Much appreciated, cheers all.
|
|
dnmalc
|
posted on 20/12/05 at 10:30 PM |
|
|
as you are just starting remember to weld it up progressively and evenly on each side to avoid heat distortion hope it all goes well
|
|
907
|
posted on 21/12/05 at 04:54 PM |
|
|
Cut 'n shut ?
Hi,
The term, "Cut and Shut" seems to be misused nowadays.
I've always understood it to mean that you cut a vee, then shut the vee, thus creating a bend.
(the pic below is taken from "The Science and Practice of Welding by A C Davies" p338)
Paul G
 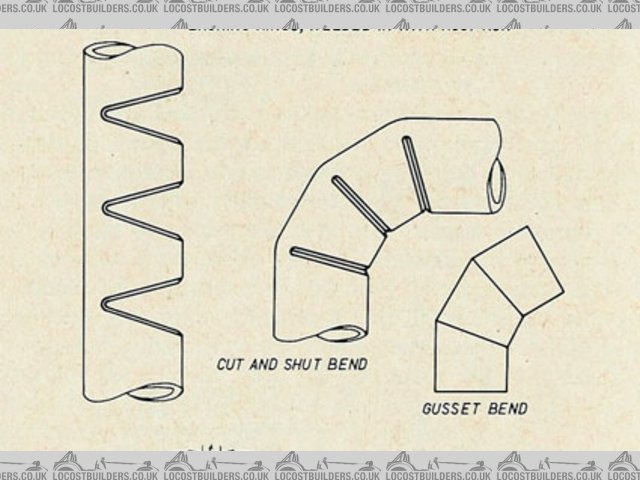 Rescued attachment cut-and-shut-s.jpg
|
|
rusty nuts
|
posted on 21/12/05 at 05:22 PM |
|
|
I remember seeing an exhaust manifold in stainless done just like that Paul .
|
|
907
|
posted on 21/12/05 at 05:45 PM |
|
|
I must remember to block that garage keyhole.
 
Paul G
|
|
ecosse
|
posted on 21/12/05 at 06:15 PM |
|
|
907: the pic shows exactly what I was thinking about doing, only using a single cut for each change of direction.
Does that change any opinions or is a complete cut and butt weld still the way to do it?
Cheers
Alex
|
|
907
|
posted on 21/12/05 at 08:48 PM |
|
|
To be honest it's easier to cut all the way through.
You can then grind or file to get a perfect fit before you tack & weld.
I use a little band saw so no trimming, just cut to the precise angle,
then weld with the TIG.
Below is a bit of the manifold that Rusty's on about. All made with 5 deg cuts.
I couldn't get preformed bends to fit. It took forever to make.
Paul G
 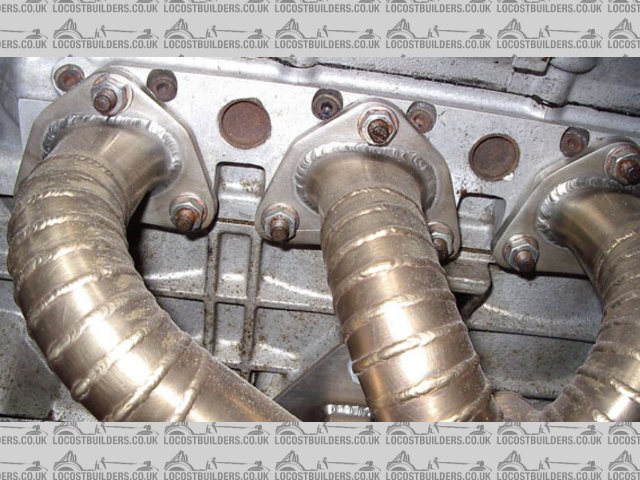 Rescued attachment manifold-cyl123s.jpg
|
|
ecosse
|
posted on 21/12/05 at 09:48 PM |
|
|
Whew...stunning bit of work, I've done similar to make a bike exhaust but it involved nothing like the work that must have gone into that!
A bandsaw would be nice (so would a tig come to that), but as I don't really have the space I'm off to buy a chop saw tomorrow (my
hacksawing skills are not the best!)
Cheers
Alex
|
|
britishtrident
|
posted on 22/12/05 at 10:42 AM |
|
|
Cutting a "V" to get a bend in a structural member is very bad practice, even if the weld is to pro standards you are still left with what
could be an unstable crack that can fail without warning. Doing 4 welds is much safer.
|
|
MikeR
|
posted on 22/12/05 at 12:53 PM |
|
|
i like that answer, as i did 4 welds 
|
|
ecosse
|
posted on 22/12/05 at 01:12 PM |
|
|
"Cutting a "V" to get a bend in a structural member is very bad practice, even if the weld is to pro standards you are still left
with what could be an unstable crack that can fail without warning. Doing 4 welds is much safer."
Good, I will get on with my cutting now. thanks everyone.
Cheers
Alex
|
|