BenTyreman
|
posted on 14/12/10 at 12:21 AM |
|
|
Broken rear wishbone
Some excessive toe-in on the rear lead to a brief investigation where it was discovered that the wishbone tube at the outer end of the rear lower
wishbone had broken off the end of the wishbone.
  Broken wishbone toe-in
  Broken wishbone toe-in
 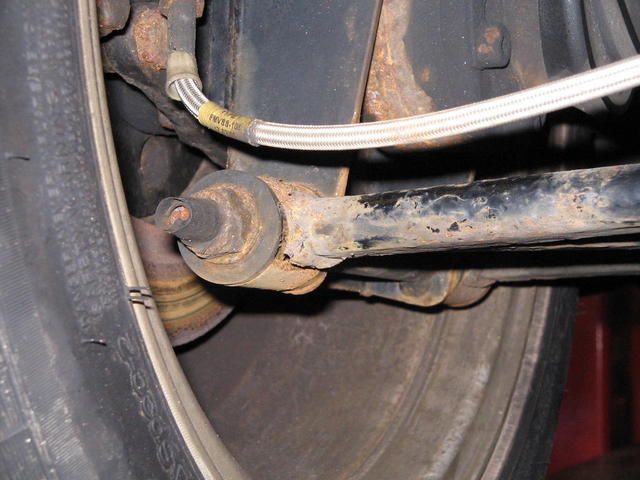 Broken wishbone
  Broken wishbone
When installed, the crush tube was approx. 0.5mm longer than the polybushes. It appears that the mild steel crush tube has rusted and glued itself to
the polybush. The wishbone has then fatigued to failure. The seam in the tube is correctly aligned with the wishbone (although not all are). The
inboard end at the front, where it is less exposed to water, is in better condition but the inboard rear crush tube is also corroded.
 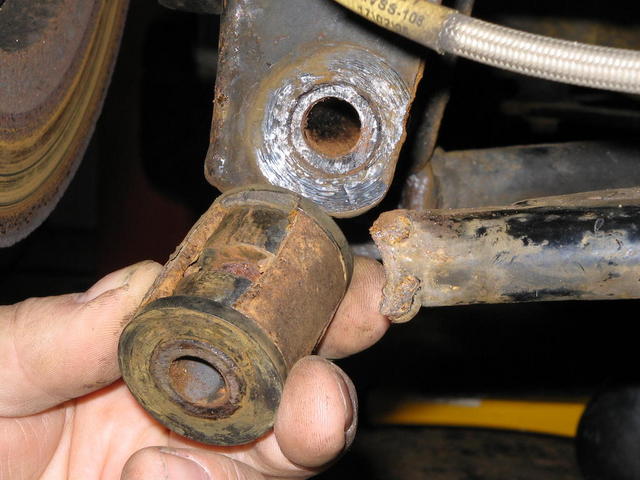 Broken wishbone tube
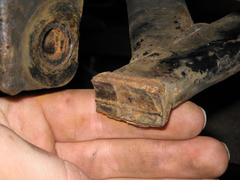 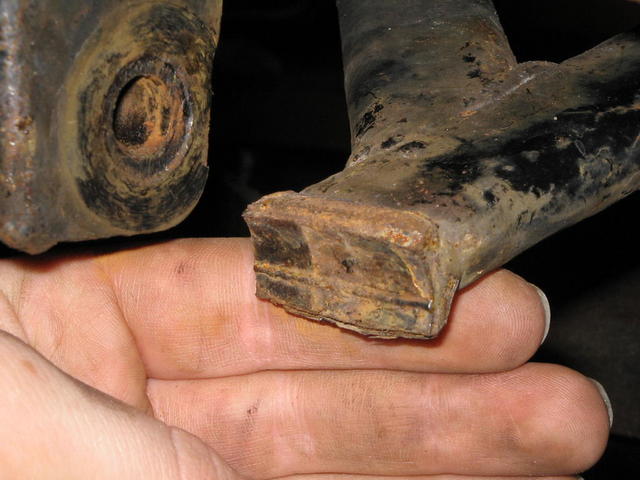 Broken end of wishbone
  Rusty crush tube
From the measurements I have taken, it appears that the MK Indy wishbones use identical polybushes and crush tubes to the Haynes Roadster. Can
anyone confirm this?
I will be replacing all of the polybushes and crush tubes with stainless tubing to prevent this happening again, and would strongly advise anyone with
mild steel crush tubes to do the same.
Being local, this looks like the best bet: Saturn
Sportscars
I also plan to use 0.5mm PTFE washers at each end of the bracket, the reduce friction between the steel bracket and the polybushes.
|
|
|
skodaman
|
posted on 14/12/10 at 12:32 AM |
|
|
I'm no expert on welding but to me it looks like a bad weld i.e. not enough penetration. Even if your explanation of the tube/bush seizing is
true I think the wishbone should bend before the weld would snap. The better makes of polybushes usually come with stainless crush tubes anyway.
Skodaman
|
|
BenTyreman
|
posted on 14/12/10 at 12:36 AM |
|
|
quote: Originally posted by skodaman
I'm no expert on welding but to me it looks like a bad weld i.e. not enough penetration.
The weld did not break, it broke either side of the weld, presumably where it was cut away by the welding and in the HAZ. There is a quadrant of
wishbone tube still left attached to the end of the wishbone, which can be identified due to the visible seam.
Edited to say that the polybushes and crush tubes were as supplied by MK Sportscars circa 2004/2005.
[Edited on 14/12/10 by BenTyreman]
|
|
skodaman
|
posted on 14/12/10 at 12:54 AM |
|
|
Ah yes I completely failed to see that. Didn't have my 3D specs on. So actually the weld was pretty good. You should really take the bushes
and tubes out once a year and lubricate it all. Don't use normal grease or it will damage the bushes.
Skodaman
|
|
907
|
posted on 14/12/10 at 07:06 AM |
|
|
IMHO
It looks to me that the whole assembly was put together with no lubrication whatsoever.
It was doomed to fail sooner or later.
Steel swells as it corrodes so joints only get tighter.
As this joint stiffened something had to give. In this case the weld.
If I remember DiySi had a similar problem. In his case the tube split.
Again IMHO, wishbones are not a "fit and forget item." Lube on assembly and check periodically.
Cheers
Paul G
|
|
Agriv8
|
posted on 14/12/10 at 07:27 AM |
|
|
Again no expert.
But the crush tube has stopped rotating ( seized up ) so the up and down motion of the suspesion has been transfered into trying to break the weakest
point.
Regards
Agriv8
Taller than your average Guy !
Management is like a tree of monkeys. - Those at the top look down and see a tree full of smiling faces. BUT Those at the bottom look up and see a
tree full of a*seholes .............
|
|
whitestu
|
posted on 14/12/10 at 08:16 AM |
|
|
Not being critical but it does all look like it hasn't had any attention in quite some time - either that or a lot of water and salt over a
shorter period.
Stu
|
|
interestedparty
|
posted on 14/12/10 at 08:28 AM |
|
|
quote: Originally posted by whitestu
Not being critical but it does all look like it hasn't had any attention in quite some time - either that or a lot of water and salt over a
shorter period.
Stu
I was thinking the same thing, but was too polite to say so
As some day it may happen that a victim must be found,
I've got a little list-- I've got a little list
Of society offenders who might well be underground,
And who never would be missed-- who never would be missed!
|
|
BenTyreman
|
posted on 14/12/10 at 09:50 AM |
|
|
The car was correctly assembled 3 years ago and has been regreased once since. It is driven in all road conditions which will accelerate corrosion,
but you do not expect this sort of problem after 11,000 miles. If this part is intended to be greased on a regular basis, then the joint should be
fitted with a grease nipple. You should not be expected to completely rebuild your suspension every 6 months. If I wanted constant maintenance, then I
would have fitted rose joints. Polybushes are sold as a "maintenance-free" option for road going cars, but clearly in this case the
materials (i.e. mild steel crush tubes) are not suitable for the job.
|
|
GeoffT
|
posted on 14/12/10 at 09:56 AM |
|
|
Next time I remove my wishbones/trailing arms I'm planning on drilling a small (3mm ish) hole in the top centre of the polybush tubes, to gives
access to the void between the two bushes. The plan is that when the damn things start up with their perennial creaking and squeeking I can get the
extension tube of a tin of WD40 or similar in there and give them a good shot of lube.
Trouble is trying to seal these holes to prevent all the crap getting in there, especlally the rear trailing arms, where access to these points would
be rather limited. Maybe a small tapered rubber peg or similar could be pushed into the holes, I'm sure I'll think of something......
|
|
Peteff
|
posted on 14/12/10 at 10:25 AM |
|
|
quote: Originally posted by Agriv8
Again no expert.
But the crush tube has stopped rotating ( seized up ) so the up and down motion of the suspesion has been transfered into trying to break the weakest
point.
Regards
Agriv8
The crush tube doesn't rotate, the poly bush does in a poly bush set up. That looks like it's rusted due to lack of
observation/lubrication/maintenance. Nothing on cars is maintenance free, we all know that and poly bushes are not sold as maintenance free or even
sold at all as standard replacement but allegedly as a better alternative. Mild steel is used in production cars and eventually rusts away but the
rubber bushes are the part that flexes and separates from the metal with less drastic results leaving a ring of metal still holding them in place as a
failsafe.
yours, Pete
I went into the RSPCA office the other day. It was so small you could hardly swing a cat in there.
|
|
procomp
|
posted on 14/12/10 at 11:10 AM |
|
|
Hi
These bushes where never designed to be used for this application. They are just cheap nasty general bushes.
I have said it before and ill say it again the UK kitcar market scene needs to have a kick up the arse and start producing and using parts that are
designed for an application rather than just using the cheap crap that they can make a BIG profit on.
If you take a look at just how many manufacturers are selling kits / cars with serious inbuilt designs and flaws that are going to result in cars
being in a dangerous unroadworthy condition at some point, the whole scene is really becoming just a joke and is now in a worse state than it was all
those years ago back in the late 70's 80's.
Cheers Matt
|
|
DarrenW
|
posted on 14/12/10 at 11:29 AM |
|
|
quote: Originally posted by GeoffT
Next time I remove my wishbones/trailing arms I'm planning on drilling a small (3mm ish) hole in the top centre of the polybush tubes, to gives
access to the void between the two bushes. The plan is that when the damn things start up with their perennial creaking and squeeking I can get the
extension tube of a tin of WD40 or similar in there and give them a good shot of lube.
Trouble is trying to seal these holes to prevent all the crap getting in there, especlally the rear trailing arms, where access to these points would
be rather limited. Maybe a small tapered rubber peg or similar could be pushed into the holes, I'm sure I'll think of something......
I was led to believe WD40 contains kerosene or something similar and therefore isnt a good long term option for lubricating such a joint. Probs no
better alternative than stripping down and regreasing with good quality lubricant. I cant help thinking that a grease nipple may not be the answer as
this wont guarantee fresh grease getting between the mating faces. Stainless crush tubes seem to make sense, as would not overtightening the arms on
re-assembly. I dont think there is a std bolt tightening torque either which ive often thought strange for such a safety critical area.
If such a thing exists maybe a rubber boot to keep out the weather would be advisable.
In some respects i have to agree with Mat. I know there are many grades of PU and some are not suited to automotive applications. Ive seen bushes
similar in ahape to those used in suspension that are sold as vibration dampers and reslient mounts for machines - not designed for the harsh
environment of road use. Ive heard of at least one kit manufacturer having a special grade of bush made, i guess its not common place though. Until a
more robust solution is available it seems like some winter maintenance is a must. If people want reliable everyday cars that require little
maintenance then kits are not really the answer.
|
|
MikeRJ
|
posted on 14/12/10 at 11:35 AM |
|
|
Look through the archives; this exact same problem has cropped up numerous times. I would not recommend mild steel crush tubes be used with these
"poly" bushes.
|
|
procomp
|
posted on 14/12/10 at 01:15 PM |
|
|
Hi
That's correct WD40 dries out and then act as more of a glue than a lubrication in this situation.
And yes again mild steel is not correct for use in this application either. Proper bushes designed for this sort of application always come with
stainless pivots.
Cheers Matt
|
|
BenTyreman
|
posted on 14/12/10 at 01:31 PM |
|
|
quote: Originally posted by procomp
These bushes where never designed to be used for this application. They are just cheap nasty general bushes.
I have said it before and ill say it again the UK kitcar market scene needs to have a kick up the arse and start producing and using parts that are
designed for an application rather than just using the cheap crap that they can make a BIG profit on.
If I could find an off the shelf alternative, I would use it. Metelastic bushes have there own problems. I will be modifying the polybushes to include
grooves to retain grease next to the crush tube and to add O-ring seals to the ends as well as using teflon thrust washers.
If these bearings won't last 10,000 miles before replacement then they should not be sold for road use. Some people might think that completely
rebuilding the suspension every 12 months or every 3,000 miles is acceptable. I don't. There is no reason that a kit car can't be used
everyday and there is no reason not to expect equal reliability to a regular car. After all, these cars have been tested by VOSA to state they are fit
for purpose.
|
|
DarrenW
|
posted on 14/12/10 at 02:00 PM |
|
|
The cars may have been tested by VOSA against specific requirements but this does not assure conformance to any warranted design techniques. It would
be a fair bet that no kits have a detailed design process, DFMEA's, NPI project management or detailed test analysis carried out during
development. If they did then few of us could afford them. Until production volumes allow such luxuries then unfortunately you have to treat the cars
as amateur built and accept the maintenance and on-road prototype developing that it gives.
It is a hinderance that the suspension will need to be stripped down periodically but if that maintains the high level of enjoyment that these cars
give then i guess its a small price to pay. Think of these cars more like vintage and classic cars rather than compare to the reliability of todays
road cars. the bottom line is that kit cars arent suited to those without a fair degree of spannering ability.
Im not saying i disagree with what you are saying by the way, over time and with continuous improvement yours may not need such a high level of
maintenance. Sounds like you have some good ideas.
Its probs worth saying that the reason others may say there cars dont need to be rebuilt so often is that they are not aware of the potential problems
and havent checked. you are aware and will have a better car as a result.
|
|
whitestu
|
posted on 14/12/10 at 02:01 PM |
|
|
quote:
There is no reason that a kit car can't be used everyday and there is no reason not to expect equal reliability to a regular car. After all,
these cars have been tested by VOSA to state they are fit for purpose.
Another way of putting that is 'Let's close down the UK kit car industry'. By definition the manufacturers do not have the budget to
make cars to the same standards as big manufacturers.
I'm not saying that your bushes weren't a bit crap [mine are the the same and are fine after 4 years], just that if we apply main
manufacturers standards to kit cars they will disappear, and personally I don't want that to happen.
Stu
|
|
interestedparty
|
posted on 14/12/10 at 02:30 PM |
|
|
quote: Originally posted by DarrenW
The cars may have been tested by VOSA against specific requirements but this does not assure conformance to any warranted design techniques. It would
be a fair bet that no kits have a detailed design process, DFMEA's, NPI project management or detailed test analysis carried out during
development. If they did then few of us could afford them. Until production volumes allow such luxuries then unfortunately you have to treat the cars
as amateur built and accept the maintenance and on-road prototype developing that it gives.
Some very sensible and true stuff there.
As some day it may happen that a victim must be found,
I've got a little list-- I've got a little list
Of society offenders who might well be underground,
And who never would be missed-- who never would be missed!
|
|
GeoffT
|
posted on 14/12/10 at 02:42 PM |
|
|
quote:
I was led to believe WD40 contains kerosene or something similar and therefore isnt a good long term option for lubricating such a joint.
Doesn't have to be WD40....!
There's a plethora of spray lubricants on the market, surely there's something out there suitable in this application.......?
|
|
whitestu
|
posted on 14/12/10 at 04:13 PM |
|
|
Anybody know what Caterham use for bushes / sleeves?
|
|
MK9R
|
posted on 14/12/10 at 04:15 PM |
|
|
quote: Originally posted by procomp
Hi
That's correct WD40 dries out and then act as more of a glue than a lubrication in this situation.
And yes again mild steel is not correct for use in this application either. Proper bushes designed for this sort of application always come with
stainless pivots.
Cheers Matt
WD40 isn't a lubricant, you need something like Q20 (shameless plug) that is a proper lubricant and water dispersant
BUt top be fair lubricant isn't what you need here, these bushes aren't designed to rotate, the rubber is supposed to flex during
rotation
[Edited on 14/12/10 by MK9R]
Cheers Austen
RGB car number 9
www.austengreenway.co.uk
www.automatedtechnologygroup.co.uk
www.trackace.co.uk
|
|
Liam
|
posted on 14/12/10 at 04:43 PM |
|
|
quote: Originally posted by MK9R
BUt top be fair lubricant isn't what you need here, these bushes aren't designed to rotate, the rubber is supposed to flex during
rotation
[Edited on 14/12/10 by MK9R]
Except the subject of this thread is not rubber bushes - it's poly bushes which are intended to rotate relative to the crush tube. 
Stainless crush tubes and grease nipples for belt and braces gets my vote.
[Edited on 14/12/10 by Liam]
|
|
MK9R
|
posted on 14/12/10 at 04:45 PM |
|
|
quote: Originally posted by Liam
quote: Originally posted by MK9R
BUt top be fair lubricant isn't what you need here, these bushes aren't designed to rotate, the rubber is supposed to flex during
rotation
[Edited on 14/12/10 by MK9R]
Except the subject of this thread is not rubber bushes - it's poly bushes which are intended to rotate relative to the crush tube. 
Stainless crush tubes and grease nipples for belt and braces gets my vote.
[Edited on 14/12/10 by Liam]
oh yeah, just realised, just saw the black and thought they were rubber :p
Cheers Austen
RGB car number 9
www.austengreenway.co.uk
www.automatedtechnologygroup.co.uk
www.trackace.co.uk
|
|
Frosty
|
posted on 14/12/10 at 04:50 PM |
|
|
quote: Originally posted by MK9R
quote: Originally posted by procomp
Hi
That's correct WD40 dries out and then act as more of a glue than a lubrication in this situation.
And yes again mild steel is not correct for use in this application either. Proper bushes designed for this sort of application always come with
stainless pivots.
Cheers Matt
WD40 isn't a lubricant, you need something like Q20 (shameless plug) that is a proper lubricant and water dispersant
BUt top be fair lubricant isn't what you need here, these bushes aren't designed to rotate, the rubber is supposed to flex during
rotation
[Edited on 14/12/10 by MK9R]
This is why I don't like poly bushes as an overall product - because there is no correct answer with all of the cheap and nasty products out
there.
Some manufacturers state that the bush is designed to rotate around the tube, and some say the rubber is designed to flex. There seems to be no right
or wrong answer - the answer you get depends on how cheaply made the bushes are.
Personally, the only way I have seen polybushes work well in kit car applications, is to treat them like a nylon bush instead. By that I mean that
everything should be a precision fit.
1) Ensure the crush tubes are an accurate fit for the rubber bushes and will rotate freely. If they are tight, adjust them. If they are loose, buy new
ones.
2) Ensure that the rubber bushes are a precision fit to the wishbone, and require very little force to insert. If they require force, it means they
are too big, and that means the crush tube hole will distort. In this case, the wishbone eye should be reamed. The weld should be ground down too.
3) Ensure the crush tube still rotates freely with the bushes fitted into the wishbone.
4) Ensure the crush tubes are stainless.
5) Ensure the crush tubes are between 0.2 and 0.5mm longer than the fitted bush.
6) Use a suitable grease, and grease the bush faces (that fit into the wishbone brackets), and the entire crush tube. I use a lith moly grease.
If you adhere to the above, you will be left with a bush which operates tightly, and cleanly with very little stiction. This ensures that a maximum
amount of force is transferred into the spring, and not the wishbone.
It also gives you a much faster reacting suspension system, which is the key to a lot of grip problems on these types of car.
|
|