ecosse
|
posted on 29/11/06 at 07:55 PM |
|
|
Wishbone weld points
As per pic below, I'm not sure whether I should weld up the end of the tubes where they finish at the BJ end and on the small vertical face of
the plate to tube area, does it matter or make a difference to the strength of the part?
If yes to the tube ends, should these be flattened or should a small fillet be welded in, or again, does it matter?
Cheers
Alex
 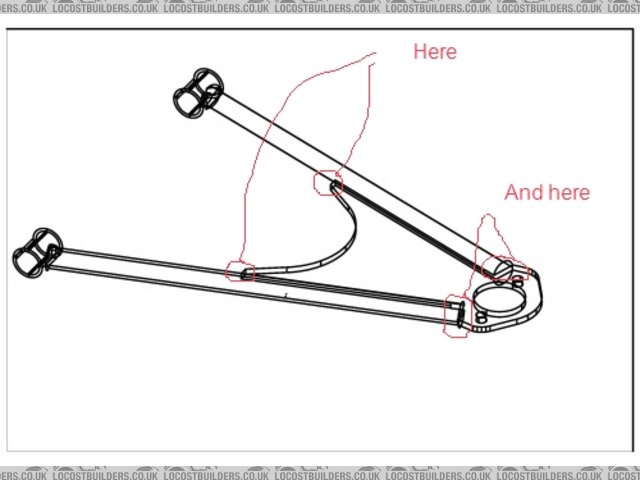 Rescued attachment bottomwishbonetest.jpg
|
|
|
nick205
|
posted on 29/11/06 at 08:30 PM |
|
|
The one shown in your diagram looks very similar to the lower front MK wishbone for the Indy. On the MK supplied item the plate si fully welded to
the tube and the ends of the tube are closed with a weld bead.
HTH
|
|
t.j.
|
posted on 29/11/06 at 08:32 PM |
|
|
I'm going to weld it.
I had the same thoughts.
But as the weld isn't around the tube it will no or less influence to the strenght
The front of the tube will be in my case will be inserted by the mountingplate.
I don't want any water or something else into the tube so i'm welding it.
grtz
|
|
907
|
posted on 29/11/06 at 09:00 PM |
|
|
Hi
I welded round the ends of the gusset plate and cut half circles and welded in at 45deg. (see pic.)
HTH
Paul G
 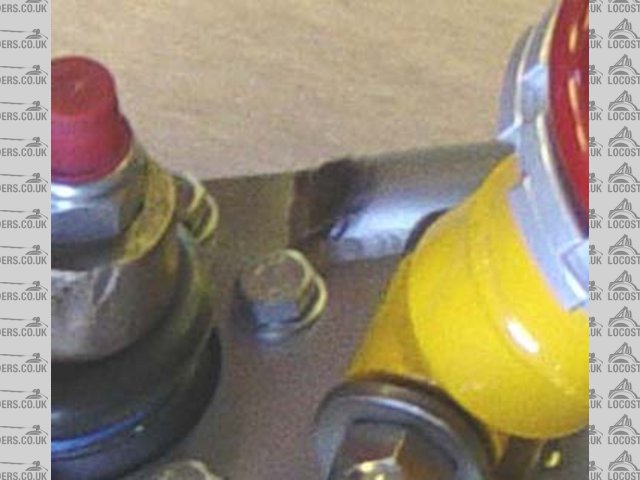 Rescued attachment w b tube end s.jpg
|
|
ecosse
|
posted on 29/11/06 at 10:34 PM |
|
|
Thanks guys , weld it is then (hadn't thought about water getting in ) and the 45deg angle and fill method looks good.
Cheers
Alex
|
|
NS Dev
|
posted on 30/11/06 at 08:45 AM |
|
|
when you finish the welds at the inner end (plate to tube) run them out away from the joint and onto the tube a bit.
Prob ott on this application but always good practice to run the weld out a bit to move the end of the heat affected zone away from the point of peak
stress. (have a look at a JCB digger's rear arm next time you get the chance, look at the flange plates on them and how they fork out the welds
from the ends of the plate onto the boom to prevent cracking)
[Edited on 30/11/06 by NS Dev]
Retro RWD is the way forward...........automotive fabrication, car restoration, sheetmetal work, engine conversion
retro car restoration and tuning
|
|
ecosse
|
posted on 30/11/06 at 11:35 AM |
|
|
quote: Originally posted by NS Dev(have a look at a JCB digger's rear arm next time you get the chance, look at the flange plates on them
and how they fork out the welds from the ends of the plate onto the boom to prevent cracking)
[Edited on 30/11/06 by NS Dev]
Damn, I used to drive JCB's (long time ago) and always wondered why they did that
As you say may be overkill but can't harm anything, Cheers.
Alex
|
|