NS Dev
|
posted on 7/5/06 at 10:37 PM |
|
|
Pics from weekend Tig play!
Been playing, steep learning curve an all that but confidence on stainless is getting much better, here's some awful pics:
Bead run on stainless, tricky to photo as its so reflective, need to sort the span control on the foot pedal, couldn't back off enough at the end
to fill the crater, and I'm no good at relying on the slopedown, just can't get used to letting the pedal go before I want to stop!!
 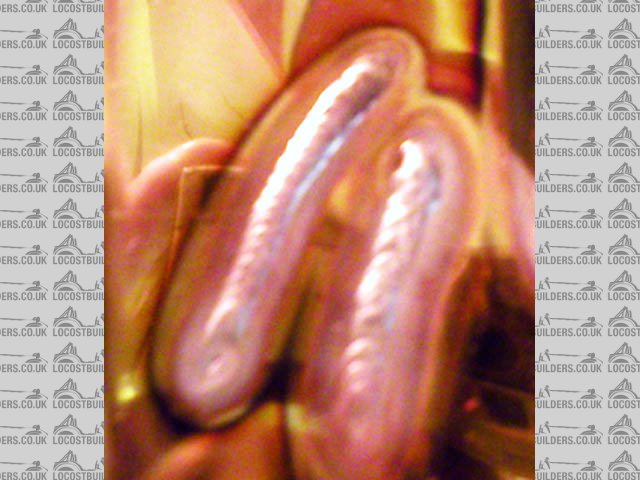 stainless bead 1
Me 2x2 " into 1 x 2.5" collector welded up. The centre part is welded inside and the outer bits on the outside, that's why the beads
stop:
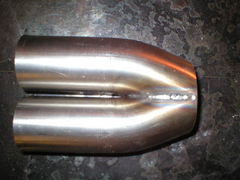 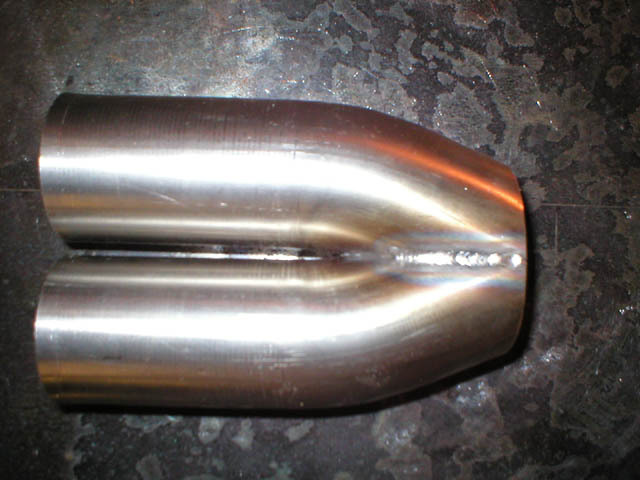 collector 1
This afternoon's hangover cure play:
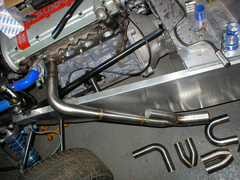 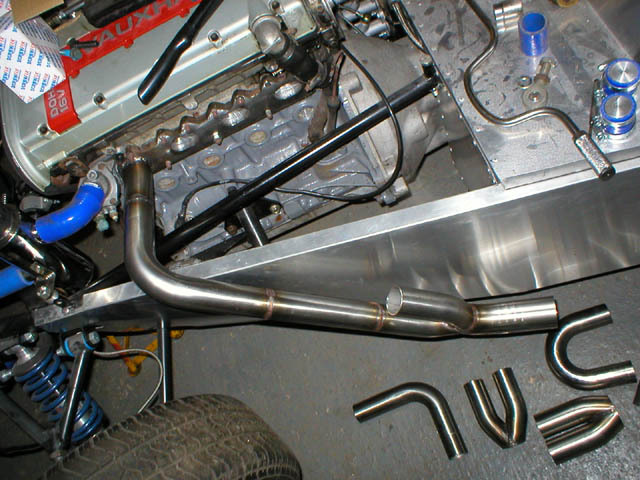 manifold start 1
and where I am at with ally, getting better but not consistent by any means yet!!!:
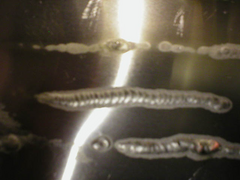 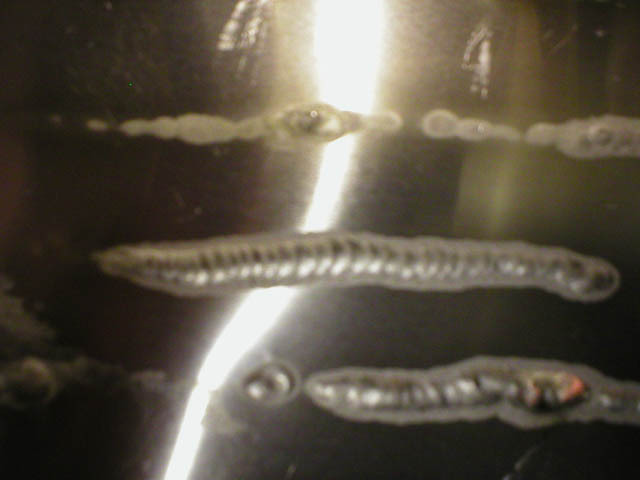 ally bead 1
And finally the machine itself!!:
[img][/img]
Retro RWD is the way forward...........automotive fabrication, car restoration, sheetmetal work, engine conversion
retro car restoration and tuning
|
|
|
James
|
posted on 7/5/06 at 10:54 PM |
|
|
TIG is soooo good isn't it!
That's looking great for just a few hours practice!
Would love to have my own TIG set. I did a City and Guilds in it a couple of years ago, went back a few months ago to TIG up my rollbar, to say my
skills had lapsed in that time was an understatement!
Stuck with the steel and it was ok eventually, though blew plenty of holes on the tricky bends.
As for the ali TIG I tried, so as to weld up the 'prototype' sender hole in my tank..... forget it! Soon realised I was about to turn a
£90 tank into a pool of liquid ali!!! So gave up and went with good old easy self tappers and sealant!!!
Good Luck with the practising!
James
------------------------------------------------------------------------------------------------------------
"The fight is won or lost far away from witnesses, behind the lines, in the gym and out there on the road, long before I dance under those lights."
- Muhammad Ali
|
|
ReMan
|
posted on 7/5/06 at 10:58 PM |
|
|
That surely is a beast!
The exhaust looks like you've done a good job to me
It sounds like not the easiest technique to learn, but invaluable when mastered.
Colin
|
|
the_fbi
|
posted on 7/5/06 at 11:48 PM |
|
|
Nice going!
I really want a tig but one to do ally with is muchos £££ 
|
|
907
|
posted on 7/5/06 at 11:49 PM |
|
|
Hi Nat
First pic looks like a couple of cocktail sausages. I like cocktail sausages.
Second one, You'd find a bit of backing gas helpful on the outside when you weld the inside.
It would come through and look as if it had been welded from the outside. Otherwise, brill.
Third? Well smart.
Number four. That's good. It's not easy welding when you haven't got a joint line to follow. again.
Five. Retake the pic so I can see the lower dials.
Slope outs work work different, depending on machine. Some work on a percentage of the amp setting,
some you set the amps you drop down to.
i.e. amps = 100. slope down set to 6 =40% drop, =60 amps.
My Lincoln at work you set what it will drop to.
i.e. set to 80, it will drop to 80.
Foot pedals are similar. Some drop to 0, some you set a percentage drop.
i.e. Set to 8 on a 1 to 10 scale, it will drop 20%.
All in all, well done
Paul G
|
|
NS Dev
|
posted on 8/5/06 at 12:14 AM |
|
|
Cheers folks!
They do look like sausages don't they! Shame the pic wasn't very good as the bead on the left was really good but for the flipping crater
on the end.
Practised for about 20 mins on steel, initially dipping the filler was tricky to co-ordinate. Then I went and did some ally, nigh on impossible was my
first impression, then I realised how incredibly clean you have to get it!! Then I went back to steel and discovered that the practise on the ally had
made my dc steel work FAR better!!
Paul - Yep, need to get a t-piece and another flowmeter really so i can do back gas, at the mo not doing it at all. I'll read up on the slope
system used on the machine. At the mo both are just set to slightly above nothing at all!
Can't work out how the machine "dial" amp setting and footpedal "dial" amp setting and the actual pedal itself all
interact. I don't know if the dial on the pedal unit competely overrides the one on the machine itself or not. I've just played about
until I could get a nice run and enough span on the pedal control to hold the puddle well.
Retro RWD is the way forward...........automotive fabrication, car restoration, sheetmetal work, engine conversion
retro car restoration and tuning
|
|
NS Dev
|
posted on 8/5/06 at 12:19 AM |
|
|
quote: Originally posted by the_fbi
Nice going!
I really want a tig but one to do ally with is muchos £££
Yep, not cheap at all, but the way i tried to justify it to myself is that a manifold from Simpson or SDW for my XE engine was going to be £700 ish.
The Stainless bends and tube cost me £150 ish and the welder was £525, plus all the other stuff like gas I suppose, but at the end of the day I have
the welder and a manifold for not much more than an off the shelf manifold.
(that's how I'm trying to think about it anyway!! )
Retro RWD is the way forward...........automotive fabrication, car restoration, sheetmetal work, engine conversion
retro car restoration and tuning
|
|
907
|
posted on 8/5/06 at 08:42 PM |
|
|
quote: Originally posted by NS Dev
Cheers folks!
They do look like sausages don't they! Shame the pic wasn't very good as the bead on the left was really good but for the flipping crater
on the end.
Practised for about 20 mins on steel, initially dipping the filler was tricky to co-ordinate. Then I went and did some ally, nigh on impossible was my
first impression, then I realised how incredibly clean you have to get it!! Then I went back to steel and discovered that the practise on the ally had
made my dc steel work FAR better!!
Paul - Yep, need to get a t-piece and another flowmeter really so i can do back gas, at the mo not doing it at all. I'll read up on the slope
system used on the machine. At the mo both are just set to slightly above nothing at all!
Can't work out how the machine "dial" amp setting and footpedal "dial" amp setting and the actual pedal itself all
interact. I don't know if the dial on the pedal unit competely overrides the one on the machine itself or not. I've just played about
until I could get a nice run and enough span on the pedal control to hold the puddle well.
Ah! The old dial on the pedal eh.
On most machines I've used you set your amps on the front of the welder. This is your maximum current, i.e. foot fully down.
The setting on the foot switch is the percentage of the main current that the pedal will drop to, before switching off.
Lets say amps set at 80
Foot pedal dial set half way (50%)
Gives you 80amps to 40amps, then off.
You wouldn't normally use the whole current range on the pedal. Just enough to let the pool solidify gently.
You would have the slope in and out switched off or zeroed, since you are using the foot pedal slope in and out anyway.
Clear as mud ?
Paul G
|
|
NS Dev
|
posted on 8/5/06 at 11:47 PM |
|
|
ahhhhhhhhhhh!!!!
Now that makes sense believe it or not!
When I first played with the machine I remember being able to run an arc so weak it only tickled the surface of 0.8mm steel. Now with the pedal right
back it is still what feels like about 40 amps, then straight off.
What you say would make sense as I have around 50% on the pedal dial and 80 amps on the machine front panel!!
AHA!!!
will play again tomorrow night!
Been welding sills on a bloody N reg nissan micra tonight, so all mig and no tig makes Nat need a flipping shower now!!!
Cheers Paul, you may have just cleared up my main remaining mystery of the machine!
Retro RWD is the way forward...........automotive fabrication, car restoration, sheetmetal work, engine conversion
retro car restoration and tuning
|
|
Syd Bridge
|
posted on 9/5/06 at 09:07 AM |
|
|
quote: Been welding sills on a bloody N reg nissan micra tonight, so all mig and no tig makes Nat need a flipping shower now!!!
Why? How often do you wash? Smelly bloody poms.
Cheers.
[Edited on 9/5/06 by Syd Bridge]
|
|
Peteff
|
posted on 9/5/06 at 09:23 AM |
|
|
Been welding sills on a bloody N reg nissan micra tonight,
I've done a few of those as well, was there anything left to weld to at the back?
yours, Pete
I went into the RSPCA office the other day. It was so small you could hardly swing a cat in there.
|
|
NS Dev
|
posted on 9/5/06 at 10:11 AM |
|
|
In the words of Paul Daniels, "not a lot" !!!!!
(but enough for MOT purposes, as I said to the chap with the car, it's not a classic restoration job, but then it's hardly ever going to
be a classic is it!!)
Can't believe it on such a new car! My 1989 sierra has less rot!
Retro RWD is the way forward...........automotive fabrication, car restoration, sheetmetal work, engine conversion
retro car restoration and tuning
|
|