MikeR
|
posted on 3/10/11 at 09:12 PM |
|
|
help designing / making shed workshop roof or roof trusses
I've got permission to make a 'shed' which should be 8' wide and 12' long (or maybe a little longer if a tree gets
accidentally cut down). The plan is to make it in 4' wide sections framed in 2"x2" and screw these together. I was also going to add
a 2x2 to the middle of the wall section. Got the sides and base all sorted in principle.
I'd like to do the apex at 2.4m and the sides at 2m. The top of the sides will have a 2"x2" batton screwed to the top which the roof
structure will rest on and the other battons will transfer the weight downwards. The sections will be screwed together (meaning every 4'
you'll actually have a 2x4) batton.
So ........... how do i do the roof?
Will 2x2 battons every 2' be strong enough with a sheet of OSB screwed to it?
Should I put a cross brace at the height of the eves ever 2' or 4' to hold the shed together?
What size cross brace?
Anything else I need to think of?
[Edited on 3/10/11 by MikeR]
|
|
|
JoelP
|
posted on 3/10/11 at 09:32 PM |
|
|
not sure if i follow exactly what you mean, but you do definately need a bit horizontal at 2m high, to prevent the roof spreading the sides. 2"
will be fine IMHO. Id just use cheap CLS timber for the sides, its about 73mmx38, so you could get 35mm over each board and not need to screw them
together.
Beware! Bourettes is binfectious.
|
|
zilspeed
|
posted on 3/10/11 at 09:34 PM |
|
|
Hang fire while I look out my pics.
I did mine in 3"x2". Actually 75x50mm O/S
Wouldn't dream of doing it in anything less for a garage. Trusses were done in that as well.
Give it 5 mins and I'll have the pics up.
Here you go.
[img]http://
  Garage 1
[/img]
[img]http://
 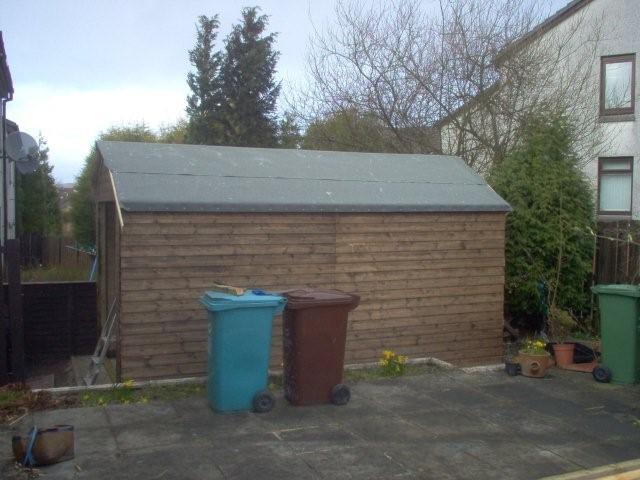 Garage 3
[/img]
[img]http://
 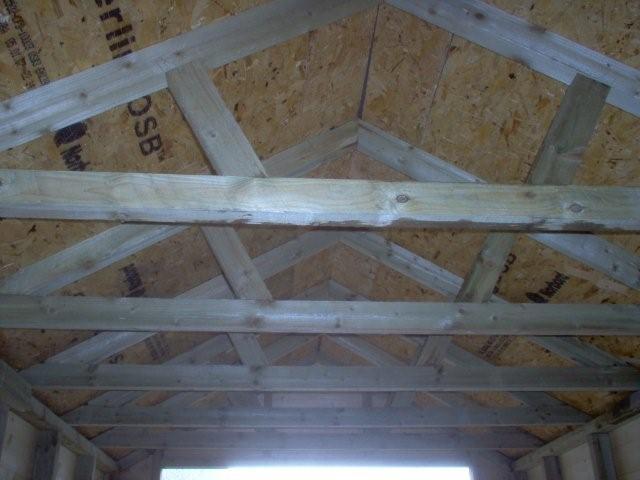 Garage 6
[/img]
I did mine in 1200mm sections.
[Edited on 3/10/11 by zilspeed]
|
|
ianclark1275
|
posted on 3/10/11 at 10:41 PM |
|
|
i used 40mm angle steel and welded trusses, and made more headroom.
Railway timber as a door lintel.
Chipwood tounge and groove floorboards for the roof (there heavy!)
im 100kg and can walk on the roof.
it has bowed over time and you can see it struggleing in photos, but its been up years now!
 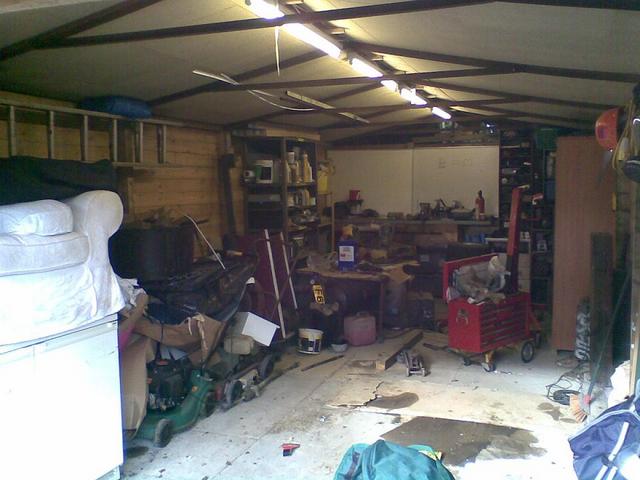 Description
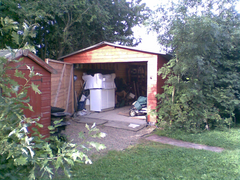 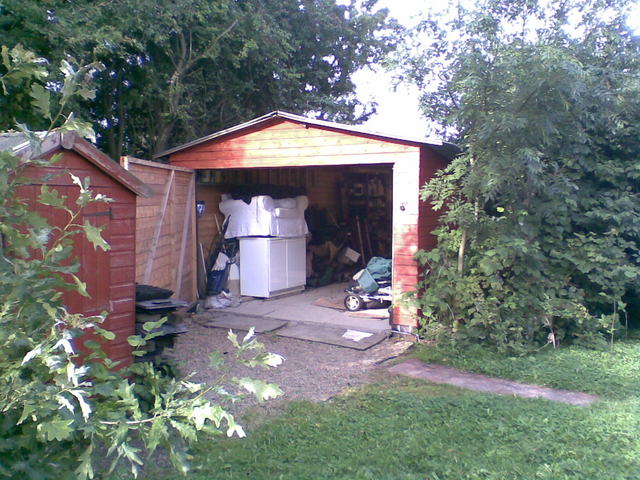 Description
measure twice, cut once, scrap it, start again.
|
|
ianclark1275
|
posted on 3/10/11 at 10:44 PM |
|
|
look at the fukŠng mess in there.
measure twice, cut once, scrap it, start again.
|
|
Bare
|
posted on 4/10/11 at 01:58 AM |
|
|
You WILL need cross ties, or the loads will spread the lengthwise walls outwards until they topple.
Ceiling joists (bottom chords to the triangles formed by the roof joists/rafters, as a simple descriptor, at Max 4' centres IE; 2 such as
Minimun for your shed.
Likely not current code but certainly so 30 years back With those youi and 3 mates can clomp around on the roof with impunity .
|
|
JAMSTER
|
posted on 4/10/11 at 06:47 AM |
|
|
roof
i bought my roof trusses on ebay for my garage, this is a lot cheaper than making them.
i do have 3 left at Ł15 each if you are interested.
|
|
jossey
|
posted on 4/10/11 at 11:39 AM |
|
|
buy one truss from someone and copy them thats what i did.
also add a few bits of roof lat under the truss along the length for extra strength.....
Thanks
David Johnson
Building my tiger avon slowly but surely.
|
|
MikeR
|
posted on 4/10/11 at 09:01 PM |
|
|
But as i'm trying to do this on the cheap - i'm back to the question.....
What sized wood do i use - is 2x3 good enough as per Zil or do i need bigger (or could i go smaller)?
Does the wood need to have an upright in the middle of the wood (making it into two triangles) or will one large triangle surfice?
Would using 9mm ply glued and screwed at the joints of the triangle be ok or should i be looking at the metal plates?
Suspect i'm going to end up 'giving it a go' and hoping during the first snow falls the roof stays on 
|
|
zilspeed
|
posted on 4/10/11 at 09:55 PM |
|
|
quote: Originally posted by MikeR
But as i'm trying to do this on the cheap - i'm back to the question.....
What sized wood do i use - is 2x3 good enough as per Zil or do i need bigger (or could i go smaller)?
Does the wood need to have an upright in the middle of the wood (making it into two triangles) or will one large triangle surfice?
Would using 9mm ply glued and screwed at the joints of the triangle be ok or should i be looking at the metal plates?
Suspect i'm going to end up 'giving it a go' and hoping during the first snow falls the roof stays on
Mike
3x2 is plenty, put them in at 600mm centres. I would never ever go smaller then 3x2. This is a not really just a shed. It's a bit more than
that, and 3x2 at 600mm is really not a spec you would want to compromise on. I wouldn't have used mine to carry a hoist at a lesser spec. By all
means, go to 4x2, but you're starting to build to a spec greater than any manufacturer would go to.
If you look at my trusses, I arranged them so that each bottom chord is divided exactly into three by the internal braces, the braces are also angled
such that they meet the rafter member of the truss at mid span. So, the rafter is split into two halves and the bottom chord is divided into three.
Without actually going and buying trusses designed and manufactured to your requirements, I reckon that's pretty good principles to apply to
your design.
9mm ply glued and screwed at all of the joints would add greatly to the strength of each joint. Gang nail plates would also be good.
For my part, I have steel angle at the side of two of my trusses which my hoist trolley runs on and there have never ever been any issues.
If I might add, I didn't come up with any of my decisions from an uninformed perspective. This is what I do for a day job.
If you follow the same principles, you really aren't going to have any issues with snow loads. You'll also notice that my trusses are set
out such that each truss is set above an upright from the main structure.
Best of luck with the build, crack on.
|
|