aitch
|
posted on 3/12/09 at 02:36 PM |
|
|
basic - very basic sketch
also been talking with the technical Guy at CFS (Alex) and on the choice of resins and cloth his opinion is that polyester resins and chopped matt
would be more than adequate, if so the costs would fall drmatically compared to woven cloth and epoxy resins.. defonately some structural tests
needed..
Im only at the thinking about it stage although anyone ready to get started i am sure Alex at CFS will be more than helpfull
aitch
[Edited on 3/12/09 by aitch]
 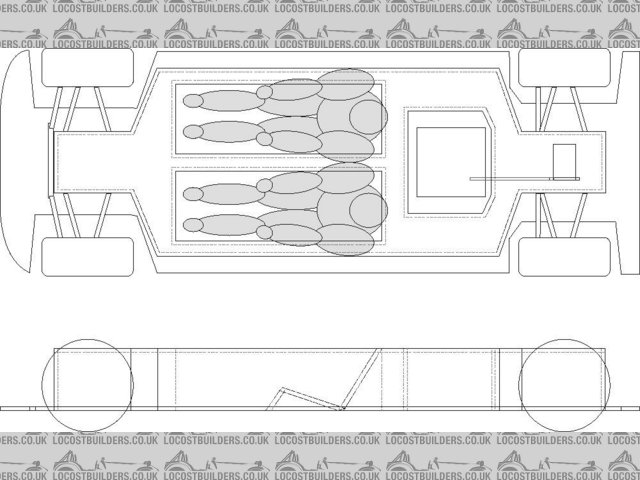 Rescued attachment Kit Car.JPG
|
|
|
kennyrayandersen
|
posted on 3/12/09 at 03:27 PM |
|
|
I’m a stress analyst working in the aerospace field with nearly 25 years of experience – maybe half of that (or better) is working with composites;
so, when I see a topic like this I feel a bit compelled to chime in. You can believe what I will tell you or not – I’m not trying to sound arrogant,
and there are people who know more about composites than me, but as a percentage of population, not so many.
quote: Originally posted by smart51
I love it when people step into this bear trap. It's even better than CEC vs BEC.
Basically, Ali is too brittle for the vibrations seen by a space frame chassis and will snap before too long. It may be all right for a car
you're going to use once (say you're entering the lemans 24hr) but not for regular use.
This of course is utter nonsense since composites are used for all kinds of airplanes, sporting equipment, and military applications where there is a
lot of abuse and vibration. In fact, one of the primary incentives for using composites is its excellent fatigue properties. It’s a matter of design
and keeping the strains below the level that any delaminations due to assorted impacts whether they be VID (visible impact damage) or BVID (barely
visible impact damage) will propagate when loaded ‘normally’. Brittleness has nothing to do with anything unless you are talking about a crash where
the material is expected to fail catastrophically, and where graphite will shatter quite spectacularly.
quote: Originally posted by Benonymous
I think a good approach with this material would be to use it partly as a structural material and partly as a core in your planning.
Where to use what requires a firm understanding of the various failure modes of the composites. The solid, as well as the sandwich material, can’t be
thrown around willy-nilly and expect it to come out OK in the end. Its really too complicated to go into in-depth in a paragraph or 2 but suffice it
to say that an engineer, or long-time composite specialist should be involved in anything more than a scooter.
quote: Originally posted by Benonymous
It would be possible to get a laminate to make a good bond with some surface prep. The choice of reinforcement I would choose would be carbon fibre.
Kevlar is an excellent fibre but it is an absolute mongrel to cut and almost impossible to sand. It fuzzes up something chronic and will drive you
nuts.
Kevlar is horribly weak in compression and so not used for any strength-type application but to line the inside of the cabin to protect the occupant
from splintering graphite (and it will splinter when crashed). It is great in tension and will strain like crazy, so it does have its place.
quote: Originally posted by Benonymous
The epoxy GRP honeycomb product is substantially cheaper than the aluminum faced types and I think it would be an excellent choice particularly if you
had it cut on a large scale CNC router.
Either is quite expensive, and I would be stunned if an aluminum facesheet/aluminum core were cheaper than graphite facesheets with a NOMEX honeycomb
core. Seriously, graphite is really expensive and even fiberglass facesheets (which I think you are referring to) on whether a foam or honeycomb core
is still quite expensive.
quote: Originally posted by Benonymous
Laser cutting isn't very suitable for aluminum; you’re better off cutting it with a rotating tool or a water jet. The GRP stuff could go on a
laser but the cost per hour compared to CNC routing is much higher. Any decent kitchen manufacturer would have a CNC router up to the job.
As to design, never feed a load into an unsupported face, only into a supported edge or corner. A good method would probably be to use the HC sheet
to make the length of the monocoque and steel to make bulkheads and suspension/engine/steering pickups and structures. The spaceframe components
could bolt to lugs or bobbins laminated into the structure.
The biggest downside to this is if you crash it and bust it, you'll have to replace the monocoque part completely.
The whole manufacturing process is complicated and expensive. And as they say, the devil is in the details. The hardest part is joining it all
together which would include specialized inserts, brackets and fittings that were specially designed for the application. Machining honeycomb is a
beotch, to say the least, but it is an essential part of the process. If can be ordered from Hexcel expanded and machined, but the cost is simply
staggering.
quote: Originally posted by aitch
as it says good pic of the palatov chassis showing the box sctions created
aitch
That chassis is simply nonsense and I wouldn’t get into it to go around the block. It shows a complete lack of understanding of load paths and proper
application of composites in general. This is a poster child for why you shouldn’t do this at home! I know this is going to come off as overly
harsh, but I believe the intent for most folks is to drive these on the road, no? The last thing you want is to be a danger to yourself and those
around you. I was simply gob smacked when I took a look at that.
NOW, let’s ask a simpler question… Why? Generally the only reason that we use composites is that we REALLY want to save some weight. We are willing
to pay huge costs and manufacturing penalties to do so; however, it should be noted that these applications are for very high-tech nearly
money-is-no-object projects that have very, very deep pockets. Think formula 1 or space shuttle.
My Eurocopter buddy was telling me that though they have the capability and ability to make a nearly all-composite helicopter (including RTM), they
are looking to use primarily aluminum on their next generation product because the cost, effort and trouble of composites are just not worth it (this
from people who really know how to do it from beginning to the end). If you are going to build an F-22 there is no way to avoid using composites. If
you are going to build a Locost, or any other home-built vehicle, IM not-so-humble O you are barking [mad] up the wrong tree!
(takes a deep breath)
Its simply silly.
[Edited on 3/12/09 by kennyrayandersen]
|
|
aitch
|
posted on 3/12/09 at 03:47 PM |
|
|
goes away to think some more
kennyrayandersen
obviously WAY more experienced and knowledgeable than i, and i always appreciate imput especially when its negative as the posibble outcomes are
horrific..
ive no idea what kind of stress analysis the petrov people have done, somehow the box sections in the chassis tub just "LOOK" right when
compared to wing spars and cockpit tubs of the homebuilt aircraft, however possibly light on structure and load paths around the suspension mounting
areas ????
aitch
|
|
twybrow
|
posted on 3/12/09 at 03:57 PM |
|
|
Some great points there Kenny - hopefully I am one of the few who does know enough to add to this - you have raised some very valid arguments. I typed
this and walked away, and you had covered most of the points I was going to touch on, so I won't repeat too much....
aitch - If you are being advised to use CSM and polyester, then the design of your chassis must be pretty pants! What is the point of going for a
composite chassis, if you don't fully utilise the benefits of composites. If you use CSM, you will add a significant chunk of weight and reduce
the mechanical performance considerably (CSM is only 1/3 the stiffness of a unidirectional material).
you seem to have designed/built that as if you were building out of an isotropic material (which CSM effectively is in X and Y directions), but
composites come into there own when you consider them as the anisotropic materials they are. Consider you load paths, and consider youravaiobale
materials, mabnufacturing techniques, inspection methods etc.
Are you doing this as a learning exercise, or to get the lightest, stiffest chassis you can? That will make a big difference to how you can progress
from here....
|
|
aitch
|
posted on 3/12/09 at 04:19 PM |
|
|
quote: Originally posted by twybrow
Some great points there Kenny - hopefully I am one of the few who does know enough to add to this - you have raised some very valid arguments. I typed
this and walked away, and you had covered most of the points I was going to touch on, so I won't repeat too much....
aitch - If you are being advised to use CSM and polyester, then the design of your chassis must be pretty pants! What is the point of going for a
composite chassis, if you don't fully utilise the benefits of composites. If you use CSM, you will add a significant chunk of weight and reduce
the mechanical performance considerably (CSM is only 1/3 the stiffness of a unidirectional material).
you seem to have designed/built that as if you were building out of an isotropic material (which CSM effectively is in X and Y directions), but
composites come into there own when you consider them as the anisotropic materials they are. Consider you load paths, and consider youravaiobale
materials, mabnufacturing techniques, inspection methods etc.
Are you doing this as a learning exercise, or to get the lightest, stiffest chassis you can? That will make a big difference to how you can progress
from here....
just to clarify, the black tub in photo's is the palatov chassis as per link's on page one of this thread, the sketch is just a very quick
ilaberation on using a similar meathod for a mid engined BEC..
my initial thoughts were to use uni and bi cloth with epoxy resins, the supplier of the honeycombe material (who's experience is with marine
applications where weight is not so much of an issue) suggested CSM... i entirely see your point about the additional weight required for strength in
this application. particularly givven the high ratio of resin when using CSM
so undoubtedly woven cloths and epoxy would be the way to go "if at all" i am in the very early stages and have to say the idea of
composites apeals to me,,,,, so does getting it right and being safe..
It could well be that i will have no option but to take a trqaditional steel frame route as i have no access to the technical expertise needed to
realise a composite chassis nor the wealth for many prototypes
aitch
|
|
twybrow
|
posted on 3/12/09 at 04:34 PM |
|
|
Thanks for the clarification.
Don't be too hasty to give up, but just have a think as to what you are aiming to achieve. You could gain plenty of knowledge by going to your
local library, and start reading! There are sooo many books out there on composite design.
Can you use a CAD package? FEA? Have you ever designed/manufactured anything in composite before?
|
|
aitch
|
posted on 3/12/09 at 04:39 PM |
|
|
quote: Originally posted by twybrow
Thanks for the clarification.
Don't be too hasty to give up, but just have a think as to what you are aiming to achieve. You could gain plenty of knowledge by going to your
local library, and start reading! There are sooo many books out there on composite design.
Can you use a CAD package? FEA? Have you ever designed/manufactured anything in composite before?
Seriously now dont laugh
model aircraft, and resesarch into homebuilt composite aircraft untill my flight training stopped 7 years ago
im not givving up on the idea and have loads of time while saving for the build
ive never used a cad package but have experience in various none 3d design packages, if i could pick up a cad package that was good enough and a
reasonable price then in time i would be able to use it
aitch
|
|
aitch
|
posted on 3/12/09 at 05:37 PM |
|
|
anninteresting article
purely a proof of concept
http://www.tech.plym.ac.uk/sme/acmc/download/chass.pdf
aitch
p.s. looking forward to months of reading and learning
|
|
twybrow
|
posted on 3/12/09 at 06:44 PM |
|
|
^ That was my dissertation supervisor back in the day! He knows his onions!
Some more reading for you:
Here
Here
You'll like this one
Here
[Edited on 3/12/09 by twybrow]
|
|
aitch
|
posted on 3/12/09 at 10:02 PM |
|
|
ooooooooooo
quote: Originally posted by twybrow
^ That was my dissertation supervisor back in the day! He knows his onions!
Some more reading for you:
Here
Here
You'll like this one
Here
[Edited on 3/12/09 by twybrow]
yes some very interesting reading and i do like that one !!!!!!
the space frame is interesting although i will have to read more to understand the mulding process, and i will be reading more
aitch
|
|
kennyrayandersen
|
posted on 4/12/09 at 12:02 AM |
|
|
I wrote that quite late at night, so maybe I was a bit grumpy; however, the points were pretty much valid. The problem with the Palatov chassis is
primarily that the vertical panels he has in the back don’t line up with anything else; so, when the load gets to the bulkhead it’s reacted as
bending, which is the least efficient possible way to do it. The reason one adds honeycomb core to two thin facesheets is to make the panel more
stable [it’s still got to carry the load]. The catch there is that when the load gets to the edges of the panel, you have only these 2 thin
facesheets to react the load. In aluminum, the bearing allowable is around 120-130 KSI ultimate, so you can make the core tapered at the edges and
form the aluminum facesheets and get away with having thin edge members.
Conversely, the composites are much worse in bearing. Without a lot of sophisticated software, you could use a value of 60 ksi (for graphite epoxy
which has been cured in an autoclave) which is around half of aluminum. Therefore, with the composite facesheets you need to [typically] add extra
plies around the boarders of the panel for bearing strength – the core still typically has to be machined, or purchased as a pre-machined detail to be
made into a composite assembly. I took a quick look through some of the links that twybrow posted and you’ll not that some of those techniques will
only work with aluminum core and facesheets, since they require the ability to crush the core or yield the facesheets in bending – nether of these are
permissible with graphite or fiberglass as it will catastrophically fail the panel. And actually it’s not such a great idea in aluminum either as the
crushed core just isn’t the same (pre-failed?).
Generally, you note that most composite race cars and such use the material to make a monocoque-type tub of sorts where the panels can be loaded
primarily in shear. The trick, then, is to get the loads which are introduced at singular points in to broader shear loads in the composite panels.
This is done with the fittings and such that I mentioned in my earlier post. It’s not that it can’t be done of course, but you will likely need your
own machine shop or be prepared to ante up to have the work done ‘out of house’.
Let’s say a decently designed and fabricated steel locost chassis weighs what? 85-100 Lb? Let’s say for the sake of argument that you’re a
über-genius such as myself (tongue-in-cheek). Maybe I could get the weight down to 65-75 Lb using finite element analysis and what I know about
composites (which as any actual genius knows – no one can know that much about anything).
What did I actually ‘pay’ to make this happen.
1. Time, initial -- extra design and analysis time
2. Money -- from something nearly any bloke with a paper route could buy to something that has to be funded by NASA – this is just with regard to
materials
3. Time , manufacturing – briefly, labor INTENSIVE. What was a couple of weekends has now gone on to a couple of months… or years
4. Facilities – where you going to get that autoclave?, or will you ‘settle’ for the lower allowables from a room temperature system? McLaren bakes,
enough said.
In summary, to save 25 pounds, you sold your soul and you left testicle to the devil (who was in the details). A body is a different story
altogether, but we are talking chassis here. If a steel chassis is good enough for the £39,275 pound Caterham Superlight 500 (and might I add
super-fast), it’s good enough for yours!
[Edited on 4/12/09 by kennyrayandersen]
|
|
Benonymous
|
posted on 4/12/09 at 06:00 AM |
|
|
Thanks for your input Kenny. There's no doubt that the good old steel space frame is pretty hard to beat. The weight comparisons you made are
really quite startling if they are accurate. So its a few hundred quids worth of steel up against thousands of quids worth of composites.
Still the garage culture will carry on and the amateurs will eventually figure out what value they can get from these sorts of materials. The main
thing that's lacking at the present time is readily available information on using composites.
By contrast, there's no end of info about steel and welding. We will have to wait until carbon fibre is used to make commonly used items and is
no longer a black art.
Personally, I'd never consider making a chassis out of composite unless I'd prototyped it in some way and possibly done some FEA in
SolidWorks or something similar.
Without people experimenting with the stuff, the average bloke has no hope of using carbon. I'd happily build something out of it if I thought
I could make it safe. I already have a vacuum bagging rig and soon I hope to have a medium sized CNC router to make moulds and plugs with.
|
|
kennyrayandersen
|
posted on 4/12/09 at 07:14 AM |
|
|
quote: Originally posted by Benonymous
Thanks for your input Kenny. There's no doubt that the good old steel space frame is pretty hard to beat. The weight comparisons you made are
really quite startling if they are accurate. So its a few hundred quids worth of steel up against thousands of quids worth of composites.
Still the garage culture will carry on and the amateurs will eventually figure out what value they can get from these sorts of materials. The main
thing that's lacking at the present time is readily available information on using composites.
By contrast, there's no end of info about steel and welding. We will have to wait until carbon fibre is used to make commonly used items and is
no longer a black art.
Personally, I'd never consider making a chassis out of composite unless I'd prototyped it in some way and possibly done some FEA in
SolidWorks or something similar.
Without people experimenting with the stuff, the average bloke has no hope of using carbon. I'd happily build something out of it if I thought
I could make it safe. I already have a vacuum bagging rig and soon I hope to have a medium sized CNC router to make moulds and plugs with.
To be sure the general knowledge about composites is much less advanced, but the conundrum is really quite a bit more complex than that. It’s not
just knowledge that is holding people back from using composites – there are a lot of factors. Just because you can do a thing, doesn’t mean you
should do a thing. In any given application there is always trade-offs and compromises. Really, this is the art of engineering. On any given
airplane, for instance, there can be found aluminum, steel, graphite, fiberglass, various adhesives, titanium, and even Velcro! The right material is
the right material regardless of whether it seems all cool and high-tech.
1) I’m fully capable of designing and even making composite parts; however, I’m not even thinking about it. Why? The biggest hurdle is cost. I’m
mean as a cost-no-object exercise in I-told-you-so, it makes a great demonstration, but I have better things to do with my time and money (as you get
older you think about things a little differently (you realize your time isn’t infinite and you’re going to need a fair pot-o-coin to get you through
the old years)). If you are sending something into space it might be worth a few thousand quid to save a kilogram of weight; if you are building a
ship – not so much.
2) The second hurdle is manufacturing. Even the above average bloke isn’t going to have, or even have access to, an autoclave. Buy the time you take
a knockdown for the room temperature cure resin system and the fact that without it you will either gain weight due to excess resin (since you will
have to use a wet layup as opposed to a prepreg (forget RTM since you’d have to make all the tools before you could make the parts and the upfront
costs are to be considered not insignificant (I actually have a friend that made a spar in his garage this way, so yes, it can be done but…)), or have
an increase in porosity, it’s even a bit less attractive. Then there is the labor. Since you don’t have a multi-million dollar tape layup machine
like Boeing, you are going to be regulated to hand cutting and laying up the composite.
If you are really dead set on having some ‘fun’ with composites, I suggest you start messing around with some fiberglass/epoxy and some rigid foam
(the kind they use in house insulation – pink or blue EPS -- Expanded Polystyrene). Start by making a hood, or maybe a se7en side door, or a se7en
boot cover, or maybe a dash (this would be great made out of glass or graphite facesheets with a foam core). As you’ve noted and as I’ve pointed out
a chassis is reserved for some highly trained and deep-pocketed ‘teams’ of people to do. A body, body panels, floors, or panels etc. are more
realistic applications that a DIY guy could expect to do and get good results. I’m not saying don’t do anything out of composites, but whatever you
do try and be sensible and realistic about it.
|
|
aitch
|
posted on 4/12/09 at 09:40 AM |
|
|
CAD FEA
Ok what sort of cost am i looking at to get a CAD package with FEA and suggestions or recomendations as to which one i should go for
aitch
|
|
aitch
|
posted on 4/12/09 at 10:35 AM |
|
|
CAD FEA OMG cough
ok had a look around at some cad packages for medelling and FEA tools to go with them,,
unfortunately way out of my price range and for a one off prototypes of chassis parts and testing to destruction would be more cost effective (along
with advise from someone in the knw to get basic design concept)
|
|
twybrow
|
posted on 4/12/09 at 01:16 PM |
|
|
You can pick up dodgy copies of most on the internet.
I used ProEngineer/ProMechanica, but it isn't the best package out there in terms of interfacing witother packages.
CATIA seems to be the most widely used CAD package, and
NASTRAN seems to be used extensively for FEA in the composites world.
|
|
Alan B
|
posted on 4/12/09 at 03:47 PM |
|
|
FEA......another hot potato
Without a good deal of conventional experience (read years of calculators and number crunching) FEA is at best just a rough guide. If, of course, you
can even get to work in the first place...most are very un-user friendly.
It's a bit like saying being able to use MS word makes you an author......just because you can churn out some nice coloured plots doesn't
make you a stress analyst.
Just a little rant in general, certainly not having a go at anyone in particular.
|
|
Volvorsport
|
posted on 4/12/09 at 04:30 PM |
|
|
www.darrian.co.uk
what do you make of these then kenny ?
www.dbsmotorsport.co.uk
getting dirty under a bus
|
|
kennyrayandersen
|
posted on 4/12/09 at 11:43 PM |
|
|
FEA packages
First, not many packages that are good at designing and solid modeling are good at FE modeling and vice versa. All of the people around me that
design use CATIA V5, which will cost you both your stones and one kidney. The package that I use for FE work is NASTRAN, which is obscenely expensive
and which also requires a preprocessor – I use PATRAN (both are MSC products) as the preprocessor (you can also use FEMAP, which is a ‘bit’ cheaper,
that some guys seem to like (my German colleague seore by it)). Each of these tools are extra ordinarily powerful, but much like a gun in the hands
of a child can do a lot of damage without proper experience and training. THere are other good packages like COSMOS etc. but the good ones, have
good support and are feature laden, so they are quite expensive, especially by DIY at home standards.
There are cheap packages, which are mostly crap, and as noted none of them are particularly easy to use. I’ve been using NASTRAN output for going on
25 years in one form or another and have been using PATRAN for maybe 15 years. The cheapest way to get to use and learn one of these packages is by
becoming a student (as stated earlier).
I wish I could tell you there is a magic button to push, or that there was some shortcut to knowledge, wealth and the attraction of stunning hotties,
but that would make me and instant liar. Even if I had a fiver for every time I saw a dysfunctional, poorly constrained and loaded and utterly
worthless [and therefore dangerous] FE model, you could just call me the Count of Monty Christo! Keep in mind these worthless models are from people
with 4-year (or more) engineering degrees and some experience – it really is that hard to do well (regardless of the advert on the FE package
website!). I really don’t think you are 1) listening, and 2) being realistic about what you are going to be able to do. If you could only channel
that determination into something that will further your understanding of the underlying principles, you’d be virtually unstoppable. I’m not trying
to dis you, make you mad or discourage you in any way. I am, given my background, trying to save you some scratch and give you some valuable [and
free] advice – this is from someone that, though not knowing much, knows a great deal more about this than most.
If you really can’t be dissuaded from diving into the pool head first, then you should consider finding a proven design and then copying it. This
might require a bit of destructive testing, but even that would be cheap compared to the path you are contemplating.
Does anyone think I’m being overly harsh here?
Darrian
It looks fine from the outside (though maybe a bit dated?). I was hoping to take a look at the chassis, but couldn’t find any pictures. In the
description, it said it used a monocoque tub, which I said in one of the earlier posts was generally the only way to go. Also, I read that March was
involved, and they have made a ton of race cars, so it probably fine structurally. Note though that my other points are all contained in this car.
It’s mostly used for racing (as opposed to the road), it’s expensive – well sorted ones were being offered at 30-40K£ which is quite apart from the
lo-cost concept. Even a roller was 20K£! This just backs up what I was saying:
1) Done by people who know what they are doing
2) Expensive
3) Difficult to produce
4) Used mostly for racing where weight-savings are critical and worth the additional cost (the small difference in weight doesn’t mean so much for a
standard road car. Additionally, the robustness (due to increased weight) is actually a desirable thing for a road-going vehicle (early Lots 7’s for
instance were very light-weight but broke easily and wore out quickly – neither of which would be a plus on a street car).
[Edited on 4/12/09 by kennyrayandersen]
[Edited on 4/12/09 by kennyrayandersen]
|
|
richmars
|
posted on 5/12/09 at 11:01 AM |
|
|
kennyrayandersen, too harsh? no, just realistic. Not that I know 1% of what you do re designing a composite chassis, but I have worked with FEA and
CFD packages so I know just how easy it is to get very pretty pictures which show what you want to see, instead of what's going to happen!
I've also made a few carbon bike frames just for fun and to learn about the process, but they're all sitting in the loft because I
wouldn't risk using them too much for the very reasons you've mentioned. If I had an autocleave, knowledge, time to make 10's of
prototypes, a test lab etc I may be able to make something I would trust but not something I did in the garage.
Carbon is a great material, and I love making things in it, but I limit it to non critical parts, like dash boards (did that about 8 years ago) and
mountain bike mud guards. On a kit car there are loads of parts that you can do in carbon which won't kill you (or someone else) if they fail.
|
|
scootz
|
posted on 5/12/09 at 11:21 PM |
|
|
quote: Originally posted by kennyrayandersen
quote: Originally posted by smart51
Basically, Ali is too brittle for the vibrations seen by a space frame chassis and will snap before too long. It may be all right for a car
you're going to use once (say you're entering the lemans 24hr) but not for regular use.
This of course is utter nonsense since composites are used for all kinds of airplanes, sporting equipment, and military applications where there is a
lot of abuse and vibration. In fact, one of the primary incentives for using composites is its excellent fatigue properties. It’s a matter of design
and keeping the strains below the level that any delaminations due to assorted impacts whether they be VID (visible impact damage) or BVID (barely
visible impact damage) will propagate when loaded ‘normally’. Brittleness has nothing to do with anything unless you are talking about a crash where
the material is expected to fail catastrophically, and where graphite will shatter quite spectacularly.
Am I missing something? Smart51 is talking about aluminium (ali) being too brittle for a spaceframe chassis and your reply stating it's
'nonsense' relates solely to composites...
It's Evolution Baby!
|
|
kennyrayandersen
|
posted on 6/12/09 at 05:24 AM |
|
|
quote: Originally posted by scootz
quote: Originally posted by kennyrayandersen
quote: Originally posted by smart51
Basically, Ali is too brittle for the vibrations seen by a space frame chassis and will snap before too long. It may be all right for a car
you're going to use once (say you're entering the lemans 24hr) but not for regular use.
This of course is utter nonsense since composites are used for all kinds of airplanes, sporting equipment, and military applications where there is a
lot of abuse and vibration. In fact, one of the primary incentives for using composites is its excellent fatigue properties. It’s a matter of design
and keeping the strains below the level that any delaminations due to assorted impacts whether they be VID (visible impact damage) or BVID (barely
visible impact damage) will propagate when loaded ‘normally’. Brittleness has nothing to do with anything unless you are talking about a crash where
the material is expected to fail catastrophically, and where graphite will shatter quite spectacularly.
Am I missing something? Smart51 is talking about aluminium (ali) being too brittle for a spaceframe chassis and your reply stating it's
'nonsense' relates solely to composites...
Mea Culpa – I did think he was talking about composites; I got confused because this thread was about a composite chassis and there was another thread
about aluminum being used, which I almost responded to, but didn’t get around to. Maybe there should have been one specifically dealing with material
selection, but regardless, my response is valid for both cases.
It’s not vibration per say that is why using aluminum MAY not be a good idea for a street frame, but rather the repeated loading at levels that will
cause fatigue cracking. Vibrations, and especially ones at a higher frequency [like that of the engine] than the natural frequency of the chassis,
tend to be at a lower level than the fatigue limit and therefore don’t do the damage. What more likely fatigues a frame are the repeated input of
high levels of applied torque from the engine as well as the repeated g-loading of just driving it down the road (those loads due to the weight of the
occupants and the engine/transmission etc.) and how those loads are reacted buy the chassis (as points near the attachment of the A-arms and the
A-arms themselves). If the Aluminum chassis is designed to keep these stresses below the fatigue limit (basically designing for infinite live) then
there is absolutely no reason you couldn’t do the chassis out of aluminum. It may not be much lighter in the end, and it will certainly be more
costly, but those are entirely different, though not irrelevant, issues.
Perhaps Smart51 used the term vibration loosely, not realizing that is actually has a more specific meaning and thus a bit different implied meaning
that what he was thinking. When we talk about vibration, we generally are referring to smaller oscillatory loads that are superimposed onto some type
of general load cycle. For instance, a car can experience up to 3g down load (due to say a dip in the road – 3g level loading is a standard on-road
load factor used in sizing over-the-road equipment)). There may be some vibration or whatnot that might be superimposed on top of that (but not
usually). A bracket might be sized for vibrations (like on an alternator, for instance), but I’m thinking for a chassis it is load cycles and not
vibrations. This 3g loading would be some type of ultimate load case – this just doesn’t happen that often (I may have experienced this only once as
a 15 year old driver while trying traverse a ditch straight on… ouch!). Fatigue loading would be maybe 1.25g or something – I’m not a car guy, I work
on airplanes and helicopters, so I’d have to do a little research to know exactly what the industry is using. Anyway, the fact that almost all of the
worlds planes and helicopters are made from aluminum suggests that vibrations are not the problem, but rather the load level that is repeated that is
at a level that does fatigue damage that is the issue.
The one thing we do know without having to get all scientific is that steel is much more fatigue tolerant that aluminum. Steel still has fatigue
issues (early 7s were plagued by cracking chassis, but to be fair they were race cars!), but it is more tolerant. Therefore, I guess the bottom line
is that it’s easier to make the frame out of steel, and more especially it’s easier for the home fabricator to get from here to there using steel for
the chassis.
|
|
Benonymous
|
posted on 6/12/09 at 09:22 AM |
|
|
One of the links in a previous post went to a .pdf file with among other things in it the chassis of the Lotus Elite. Now while I'm not going
to pretend that it was built in a felt-roofed shed in the back yard of a semi in Finchley I'd venture to suggest that it was designed with a
fairly basic set of tools where load and stress was concerned. One stand out characteristic was that the suspension mountings used to fracture, not
good... However let's say for the sake of example that I decided to build a Lotus Elise chassis from Carbon fibre and epoxy resin, using the
appropriate layup thicknesses etc. Surely this would produce a superior wet layup than glass and polyester? If this is so, then I would have a
stiffer, stronger chassis than an Elite? So maybe I wouldn't have to limit my carbon fabrications to cosmetic parts?
I respect your knowledge and understanding kenny but ultimately, experimenters will do things that engineers would never dream of and maybe even put
themselves at risk in the process. I feel that this is the way of advancement. Without these risk takers there would be no kit cars or kit planes,
ultralights or even the superb Britten V1000, made by a complete amateur in the field of engine and motorcycle chassis design. Sure, John Britten
could have crashed and died on the first corner but thanks to a bit of judicious over engineering, the concept survived and went on to be one of the
most heroic efforts in motorcycle racing of all time. Any engineer would have told him he was loopy and to give it all up and grow Petunias!
What a dull world it would be if he had eh?
|
|
Theshed
|
posted on 6/12/09 at 11:06 AM |
|
|
I love this thread. It is fantastic when the internet brings together really useful knowledge and debate and avoids unnecessary unpleasantness just
because the contribtutors disagree.
Please keep posting Kenny experience like yours is priceless. I doubt that you will put off us loonies that depart from the steel spaceframe (that is
clearly the obvious amateur choice) so any tips you can give to save us from our own insane choices.
I have made all of my own inserts for my (aluminium) honeycomb chassis. All pure guesswork. I would love to see how it is done in the aircraft
industry. Any photos anyone?
|
|
kennyrayandersen
|
posted on 6/12/09 at 01:41 PM |
|
|
quote: Originally posted by Benonymous
One of the links in a previous post went to a .pdf file with among other things in it the chassis of the Lotus Elite. Now while I'm not going
to pretend that it was built in a felt-roofed shed in the back yard of a semi in Finchley I'd venture to suggest that it was designed with a
fairly basic set of tools where load and stress was concerned.
One stand out characteristic was that the suspension mountings used to fracture, not good... However let's say for the sake of example that I
decided to build a Lotus Elise chassis from Carbon fibre and epoxy resin, using the appropriate layup thicknesses etc. Surely this would produce a
superior wet layup than glass and polyester? If this is so, then I would have a stiffer, stronger chassis than an Elite? So maybe I wouldn't
have to limit my carbon fabrications to cosmetic parts?
The point being that those basic tools include basic engineering skills; which even when present is no guarantee there won’t be trouble – this is why
even the largest, most sophisticated technology companies in the world have to test after the initial engineering work is done. Sure, graphite will
give both a stronger and lighter structure than fiberglass, since it has a higher modulus, but basically any material short of peanut butter can be
made to work – some materials are better than others. I saw a 100 year old race car powered by an enormous antique airplane engine. It is still
being raced and the frame is made from Ash (the original frame!)!
quote: Originally posted by Benonymous I respect your knowledge and understanding kenny but ultimately, experimenters will do things that
engineers would never dream of and maybe even put themselves at risk in the process. I feel that this is the way of advancement. Without these risk
takers there would be no kit cars or kit planes, ultralights or even the superb Britten V1000, made by a complete amateur in the field of engine and
motorcycle chassis design. Sure, John Britten could have crashed and died on the first corner but thanks to a bit of judicious over engineering,
the concept survived and went on to be one of the most heroic efforts in motorcycle racing of all time. Any engineer would have told him he was loopy
and to give it all up and grow Petunias! What a dull world it would be if he had eh?
You make is sound like engineers are all a bunch of chicken $hit$, which may well be true! but I believe it to be only partially true at best.
Lilienthal, was a scientist and also a great glider experimenter in the early [pre Right brother] flight days. He, of, course, augured in and was no
more. Mark Donahue also comes to mind; he was an engineer and very successful race car driver who unfortunately met an untimely demise racing in his
own creation as well. So even IF the knowledge is there, giant screw-ups can still cost you big time. I’ve got not a problem in the world with
people trying any random, dangerous and even crazy concept; the only slight hiccup in the natural selection process however is that the ‘weak’ some
times take out the strong in the act of removing themselves from the gene pool. Usually this is preceded by the expression “Hey y’all, watch this”.
The post of the motorcycle contains just a bit of irony as the riders of such are frequently referred to as organ donors. Hmmm…
Don’t misunderstand what I’m trying to say here. I’m not saying don’t do it, I’m saying educate yourself before you do (not you in particular, but
anybody wanting to go off and be extra ‘creative’); do that the best you can. Also, understand that you might be doing just to say you did i.e. it
not the best way to do it even though it CAN be done that way. Last time I check the UK was still free enough that you can spend you hard earned cash
on whatever your little heart desires; people have gotten less for more. Knowing what I know I can’t recommend it, that’s all.
You may not be able to get a formal education, but if it’s within you capability, learning new things never hurt anybody, eh? Knowledge is power.
I’m able to demand (and receive) some pretty decent compensation in my work because it’s kind of complicated and there are few that have paid the
price to acquire those specialized skills. I always tell young people that you should do, for a profession, the hardest thing you brain will allow
you to do. Lots of people are good with their hands, or artistic, but there will, for the foreseeable future, be a shortage of people that can solve
complicated problems. If you can’t do that, try and get a skill that is specialized so that you can make a decent living (actually this is one thing
that better about the European education system as compared to the US IMO).
Anyway, sorry about the rant -- it just happens that I know a bit about it and I thought I would share.
|
|
|