02GF74
|
posted on 12/11/07 at 01:52 PM |
|
|
GRP inlet manifold - why not?
Why can't an inlet manifold be made from glass fibre?
I can think of 2 reasons:
a) temperature - but CF disc brake run up to red heat so there has to be high temperature resin?
b) reistance to petrol - not sure about this but again there may be some resin/coating that could be used on the internals.
Or some other reason?
Anyone tried this?
|
|
|
Volvorsport
|
posted on 12/11/07 at 01:53 PM |
|
|
yes , most bmw run(race series i cant think of) with a composite intake , ive even made a few .
www.dbsmotorsport.co.uk
getting dirty under a bus
|
|
02GF74
|
posted on 12/11/07 at 01:57 PM |
|
|
hmmm, interesting - you say composite - what are the ingredients?
Do you have any photos/more info?
So why are people paying £ 200 for TIG welded aluminium manifold when they could make one from toilet rolls and some GRP?
Surely that is the locost way and you can curve the tracts for better flow, am i missing somehting..?
obvioulsy the male mould need to come out but that could be made up with wax or other material that can be melted out/dissolved at low termperature.
|
|
Agriv8
|
posted on 12/11/07 at 02:13 PM |
|
|
I hope CF is ok !!!!
.
Unsure if this is prepreg or not. I know mine came from Act Performance
PS it copes well with V8 heatsoak very well.
PPS Yes I work in a mess
HTH regards
Agriv8
Taller than your average Guy !
Management is like a tree of monkeys. - Those at the top look down and see a tree full of smiling faces. BUT Those at the bottom look up and see a
tree full of a*seholes .............
|
|
Werner Van Loock
|
posted on 12/11/07 at 02:16 PM |
|
|
there are a few problems to overcome. First is vacuum, it needs to withstand the vacuum generated when you let go of the throttle, so bodies close and
piston speed high means high vacuum
Second is to make the mating surface to the enngine head airtight. GRP tends to distord under temperature and after it's released from the
mould. Need some rubber type gasket and even then it's a pain to make it shut.
3rd You can't use carbon fibre for it as most heads nowadays are alloy and those 2 don't mix!
And I think because of these problems a GRP manifold turns out to be more expensive then a 1 hour aluminium jobbie
http://www.clubstylus.be
|
|
Werner Van Loock
|
posted on 12/11/07 at 02:17 PM |
|
|
quote: Originally posted by Agriv8
I hope CF is ok !!!!
Agriv8
BTW, this is not a manifold, but a plenum chamber, something completely different.
And CF is not ok if it's in direct contact to the alloy!
http://www.clubstylus.be
|
|
nitram38
|
posted on 12/11/07 at 02:20 PM |
|
|
I think I saw some Titanium fibre/resin inlet manifolds on Martin Bell's BMW (BTCC).
Not exacltly locost though!
|
|
twybrow
|
posted on 12/11/07 at 02:24 PM |
|
|
Why do you say carbon and alloy can't be used together? You would just need to insulate the carbon with a thin layer of glass.
You could definately make a composite intake. You need to pick a high temp and chemically resistant resin. The warping issue could be minimised by
good design and processing. The really tricky bit comes with getting a good finish inside and out -not really a project for a garage build!
Oh, and the reason carbon brakes can take such high temperatures, is because they tend to be made from 'carbon/carbon' composites. This is
a specialiost composite that uses very high temperature gases over the top of a stack of materials (the preform). As the hot gases touch the carbon,
they depoit themselves on the carbon as solid material. This forms the basic carbon-carbon composite. The trick is to then also include materials that
restict the oxidation of the material at very high temperatures. This is where silicon-carbide or boron-carbide are introduced, to delay the oxidation
proces until very high temperatures.
[Edited on 12/11/07 by twybrow]
|
|
scutter
|
posted on 12/11/07 at 02:31 PM |
|
|
I've just got a st170 manifold, it's definately a composite material.
 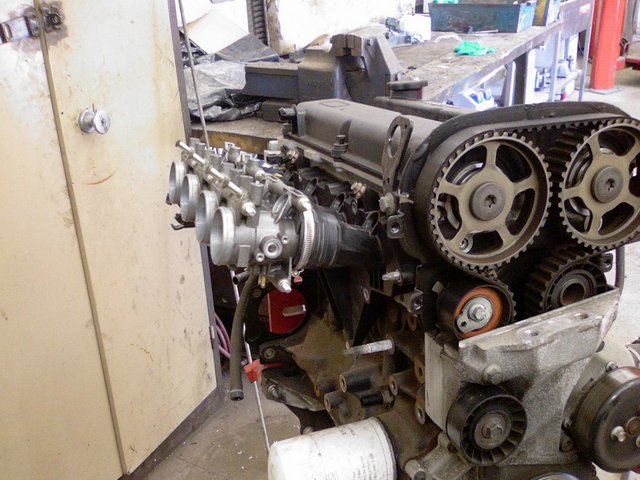 zetec throttle
The upsides are it's light and easy to work, haven't found any downsides. i'll let you know if any arise.
ATB Dan.
The less I worked, the more i liked it.
|
|
Volvorsport
|
posted on 12/11/07 at 02:41 PM |
|
|
www.absmotorsport.net
www.dbsmotorsport.co.uk
getting dirty under a bus
|
|
MikeRJ
|
posted on 12/11/07 at 02:50 PM |
|
|
Several modern car engines use plastic manifolds, the small petrol VAG engines and Rover K series spring to mind.
|
|
twybrow
|
posted on 12/11/07 at 03:16 PM |
|
|
Production parts tend to be thermoplastics. Generally, they are able to withstand much higher temperatures and are cheaper and quicker to process in
large volumes.
|
|
chriscook
|
posted on 12/11/07 at 03:22 PM |
|
|
They also need to be able to withstand a backfire - ie explosion - inside of them without exploding sending shrapnel into your face.
I did some backfire tests on plastic manifolds a few years ago. Basically we filled the manifold with oxygen and propane I think it was and stood well
back before setting it off. Most of the site at work (think airfield size) heard the tests happen.
|
|
02GF74
|
posted on 12/11/07 at 03:25 PM |
|
|
... and did they withstand the back fire?
|
|
twybrow
|
posted on 12/11/07 at 03:46 PM |
|
|
Now that is a job I want! Destructive testing by explosion! Sounds good.
|
|
awinter
|
posted on 12/11/07 at 04:12 PM |
|
|
Peugeot late s16 engines, and late 1.9 8v engines had plastic manifolds.
I think they were made from glass filled nylon. But you can also add talc, not bath talc to poly prop to make it resist higher temperatures. I used to
work at a plastic injection moulding company!
|
|
Syd Bridge
|
posted on 12/11/07 at 04:30 PM |
|
|
I've been making carbon composite intakes since 1989. Yes, that long ago.
Getting the head seal is no problem, and a good gasket solves the isolation problems.
The prepreg is high temp cure, and then post cure to bring it's Tg point (from hard to putty) up to over 200c. Glass will do the job, and I use
it regularly on budget and non cosmetic items. The main thing is to get the right resin system.
It can be done, has been done, and will continue to be done. Just don't listen to the 'can't do' people, and find out how you
'can do'. That's how I work, anyway.
I'll get carbon throttle body/intakes going soon as single entities. Just put as many together as you want and need. Time is all I need. 
Cheers,
Syd. 
|
|
02GF74
|
posted on 12/11/07 at 04:32 PM |
|
|
i realise that modern cars e.g. zetec have non-matel manifold - nylon/plastic whatever but I am propose to use GRP - olyester resing and glass matt so
is that gonna be that same?
surely if the manifold is made tick enough 1 cm? then is should resist explosions?
|
|
Syd Bridge
|
posted on 12/11/07 at 04:37 PM |
|
|
There's no poly resin that I know of that will do the job safely. The best is Scott-Bader 272, and that has a Tg of only 85c at best, and
that's with post cure.
Cheers,
Syd. 
|
|
chriscook
|
posted on 12/11/07 at 05:20 PM |
|
|
Didn't say it can't be done just pointing out something that needs to be thought about.
I think they all did survive the explosion - i can't remember too much about the test setup to be honest. Although the manifold was in a metal
cage with thick polycarbonate screens.
I think it was probably bolted down to a flat piece of steel with fuel rail, injectors and throttle body all attached then filled with the gas through
valves in the steel plate.
|
|
twybrow
|
posted on 12/11/07 at 05:26 PM |
|
|
Syd - I think the point some of us were making was that it would need a lot of thought as it was not really a suitable process for a novice laminator
to attempt, nor is GRP really the right material to do it with. Your first line 'I've been making carbon composite intakes since
1989.' Well by the sounds of it, 02GF74 hasn't!
There are resins that will allow temperatures over 200C (Crestapol from Scott Bader for example), but you would be better off using an epoxy based
system (probably prepreg based as you say).
|
|
Syd Bridge
|
posted on 12/11/07 at 05:42 PM |
|
|
If I'm having to use a 'wet layup' system, then I normally use tooling resin (epoxy). This is easily procured from most of the
composites materials resellers.
Even a novice should be able to achieve fair results, using vacuum. All depends on how the tooling is made. That is where the time and experience and
skill comes in.
Have a go. The worst can happen is it's a balls up. Then you can have another go. That's half the fun!
Cheers,
Syd. 
|
|
Volvorsport
|
posted on 12/11/07 at 05:46 PM |
|
|
the part i linked is actually a BMW one made from polyester resin , used on quite a lot of race cars .
its only carbon layup to look nice .
we made some GRP flanges aswell .
you could use the original flange , cut the tubes off after the injectors and have em machined so the grp fits snugly inside and use a high temp epoxy
glue , quite simple really .
jenvey ram pipes are glued into ally flanges .
www.dbsmotorsport.co.uk
getting dirty under a bus
|
|
twybrow
|
posted on 12/11/07 at 05:46 PM |
|
|
True true. Learning is half the fun!
Buy some cheapo polyester laminating resin, get yourself some glass and make some bits and pieces. Its useful stuff to have around anyway for repairs
to other items.
Syd - I think the worse that happens could be a rather large (and noxious) exotherm based fire!
|
|
Volvorsport
|
posted on 12/11/07 at 06:01 PM |
|
|
Stuff i made .LOL about 7/8 years ago
[Edited on 12/11/07 by Volvorsport]
www.dbsmotorsport.co.uk
getting dirty under a bus
|
|