mark chandler
|
posted on 23/8/09 at 10:37 PM |
|
|
Sierra diff rebuilding, well nearly!
Hello
I need to gear up my BEC so sourced some 3.38 bits had a go at pulling the Sierra 3.65 LSD apart, it was actually very painless, despite lots of
negative info when googling you should be able to do this with a few hand tools.
No need for a photo showing how to get the back off, just a handful of torx bolts.
So as its a LSD diff with fixed output flanges rather than snap rings I took the back off and located the circlips that hold the output shafts in
place:
 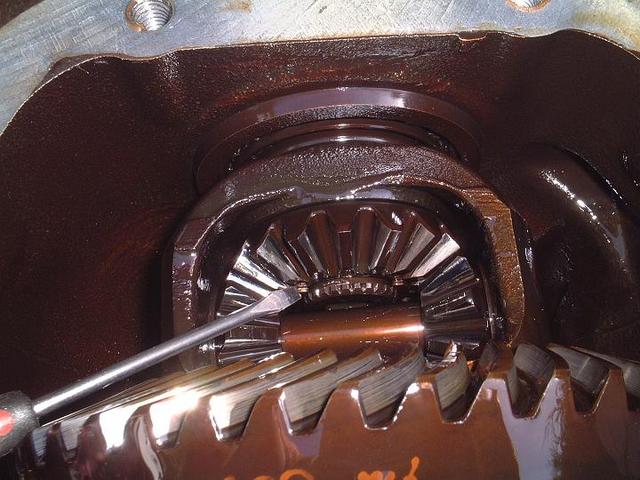 Circlip inside diff
Simply knock these into the housing and the shafts come out the side, job done.
The crown wheel assembly is held by taper bearings, these are adjusted at the side, the book shows a special tool required to unscrew the adjusters, I
found a bit of rod does the job just as well, I also needed to apply a little heat from a blow torch to the outside casing and some WD40 to help
things along then they just spin out. Do not get too hot as there is a rubber 'O' ring to stop oil leaking out.
 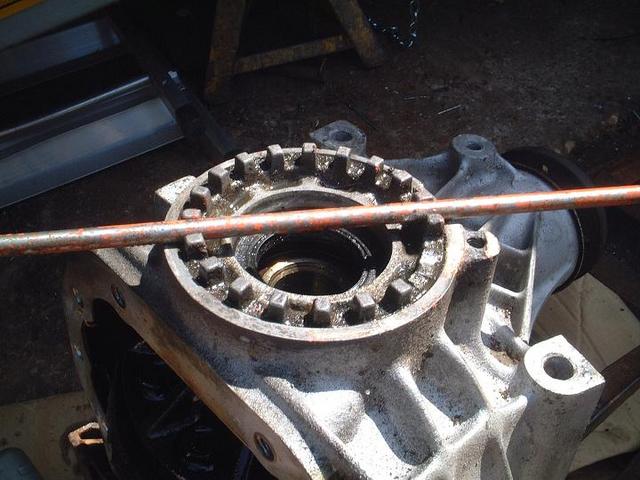 Rod on teeth.JPG
You will note a couple of teeth missing, tried with a hammer and cold chisel and snapped these off in quick order, best avoid this approach.
This then allowed me to pluck out the crown wheel assembly so turned the diff over and started on the pinion, you will need a puller here once the
flange nut is off
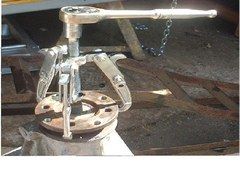 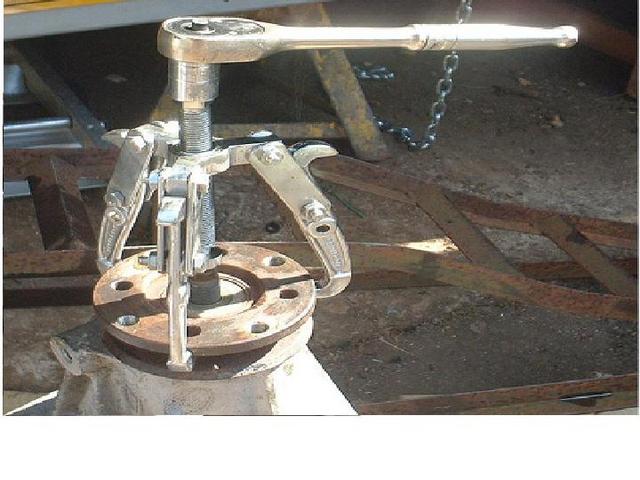 Pinion_flange
Now it all went wrong.... the 3.38 pinion I had been sold was not the same , balls so reversed everything and restored to the car..... .
I did take the oppurtunity of taking out any backlash in the gears with the adjusters, did this by hand just drop in the crownwheel and adjust with a
lot of backlash but wind in the adjusters on the side to remove any play in the crown wheel bearings.
Now twiddle each adjuster in/out together until there is a tiny amount of backlash in the gears. Okay its not 18n.m torque but a 150,000 mile diff
going for a few track days it will not really care.
Every cloud and that though, when putting the prop back it felt a bit funny, looked at the front and the bolt that holds the engine sprocket adaptor
had sheared, last time I drove this was 100mph at Woodbridge two weeks ago so very lucky the prop did not fall off on the track... gulp.
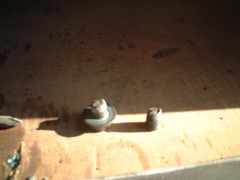 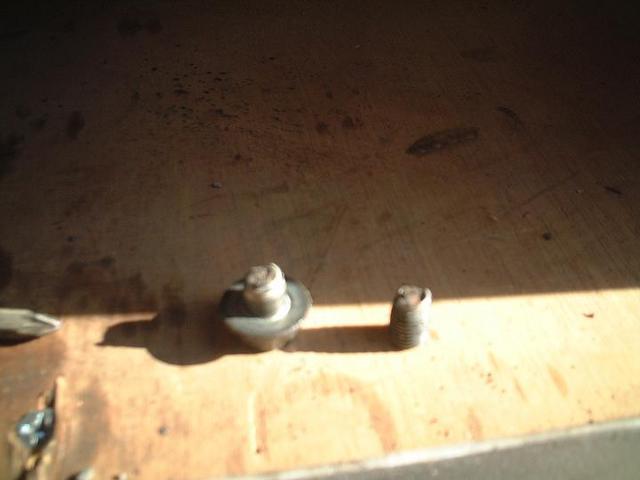 Adaptor bolt broken
So a wasted day in some respects but a lucky find, this is a proper Honda bolt, it now has a super high tensile Alan bolt in its place.
Regards Mark
|
|
|
alistairolsen
|
posted on 24/8/09 at 06:50 AM |
|
|
Useful info, I have just got a cossie 4x4 diff and I want to replace the bearings in it before I fit it. I need to know how to set the preload and
backlash correctly tho
My Build Thread
|
|
flak monkey
|
posted on 24/8/09 at 06:59 AM |
|
|
I would upload the manual but its too big, U2U me your email and I'll send you a copy.
Getting the actual diff out isnt the tricky bit. Its if you have the pinion out, you then need to set the preload on that and need some special
measuring gear.
David
[Edited on 24/8/09 by flak monkey]
Sera
http://www.motosera.com
|
|
aaron bassett
|
posted on 24/8/09 at 07:22 AM |
|
|
could you host it on mega share i would love a copy pls
|
|
mark chandler
|
posted on 24/8/09 at 07:59 AM |
|
|
18nm.ft is not a lot though, easy to turn by hand not 18nm/ft, you can do this with a spring balance just need a bit of maths on the leverage if you
pull down using the pinion flange bolt holes.
The backlash is something like .005", so barely perceptable.
On the basis that I am not building to do 100,000 miles I am not going to worry that much myself.
|
|
flak monkey
|
posted on 24/8/09 at 08:29 AM |
|
|
I will upload the manual onto my website tonight if i remember.
Sera
http://www.motosera.com
|
|
coozer
|
posted on 24/8/09 at 08:46 AM |
|
|
Err, excuse my ignorance and educate me if I'm wrong but that looks like a standard open diff, not an LSD. Am I right?
1972 V8 Jago
1980 Z750
|
|
flak monkey
|
posted on 24/8/09 at 09:41 AM |
|
|
quote: Originally posted by coozer
Err, excuse my ignorance and educate me if I'm wrong but that looks like a standard open diff, not an LSD. Am I right?
Nope, they look pretty much the same from that angle.
The viscous part is inside the part where the crown wheel is bolted on.
David
Sera
http://www.motosera.com
|
|
alistairolsen
|
posted on 24/8/09 at 09:48 AM |
|
|
Had a read of the manual and it all makes sense and should be possible barring the lack of ford tools All the pullers and stuff can be arranges,
but the measuring block and that guage pin wont be possible to replicate
My Build Thread
|
|
BenB
|
posted on 24/8/09 at 03:33 PM |
|
|
http://www.fordscorpio.co.uk/manual/rearaxle/DiffOverhaul.pdf
any use?
|
|
mark chandler
|
posted on 24/8/09 at 08:34 PM |
|
|
To my mind if you are building up a brand new diff then you may need the correct tools, however I suspect you will have an old diff with knackered
bearings and well bedded in crown wheel and pinion so its not so critical, how many donor diffs as removed will meet the build criteria?
If you are building for a heavy standard car expecting to cover 100k miles then you need it right, building for a little car, 1/4 of the weight which
will probally do no more than 20k miles then why worry so much?
When I raced landrovers we used to build the diffs tight, ie wind the side bearings in so that the bearings were just starting to bind and back off a
tiny bit, then push the crown wheel into the pinion so its binded to the point that it was hard to turn by hand. Sounds horrible but saved the teeth
chipping as you land and the crown wheel flexed, infact you could get the casing modified to place slippers behind the crown wheel to keep it loaded
on the pinion.
For this no need to go that far but 0.005 backlash is teeth meshed very closely, you can feel this when turning the pinion once you overcome the
stiction of the oil seals.
If you try and lever the assemble left or right within the housing it should not move, again should spin easily once you overcome the stiction of the
oil seals.
For track days or a BEC you want it a bit tighter as you will be slamming from idle to full power, sliding about etc, this means you will quickly be
loading/unloading the diff so any backlash will just be pushed up the drive chain.
The point I was really trying to make is that you do not need special tools to strip and put one of these back together, just a bit of common sense
and hand tools.
Regards Mark
|
|