Wingnut
|
posted on 24/6/04 at 11:59 AM |
|
|
Which is strongest ?
Would appreciate some opinions on this one, I'm remaking some suspension pickup brackets. these are basically U brackets, bolted to the
chassis.
The ones supplied with my kit are bent from 5mm steel (It's a V heavy car!)
I'm re-making the brackets to change the geo. I can weld 5mm flat steel, but there's no way I can bend it.
So is a welded 90 deg bend as strong as a bent one??
|
|
|
Mk-Ninja
|
posted on 24/6/04 at 12:28 PM |
|
|
In theory it should be stronger but it depends how good a welder you are.
I'm sure I've got one, just don't know where I've put it
|
|
blueshift
|
posted on 24/6/04 at 12:51 PM |
|
|
try cutting half way through (or a bit more) and hammering the bends over, then welding over the outside. I have seen this method reccomended.
cue mark allanson to tell me it's not the best way.. 
|
|
JAG
|
posted on 24/6/04 at 01:04 PM |
|
|
Bending will give a stronger product.
The problem with welding is the heat affected zone around the joint and the stress raiser caused by the joint between the filler and parent metal.
The weld/filler metal is usually upto the job but the heat used during the welding anneals/modifies the structure of the parent metal either side of
the joint. Welds normally fail at the fusion line between the filler and parent metal.
Welded parts are only as strong as the original metal if they are carefully ground down and then heat treated after welding.
Justin
Who is this super hero? Sarge? ...No.
Rosemary, the telephone operator? ...No.
Penry, the mild-mannered janitor? ...Could be!
|
|
Bob C
|
posted on 24/6/04 at 01:26 PM |
|
|
If you're bending you will probably weld it to tha chassis along the bend line anyway! Cutting 1/2 through WILL make it crack at the bend,
you're better putting it ina big vice & twatting it with your biggest hammer, mild steel at 5mm will bend just fine. Heating to red hot
would be preferred but that's probably not an option - you can't then use a vice or a bender anyway, you'd need a special tool.
cheers
Bob
|
|
Peteff
|
posted on 24/6/04 at 02:27 PM |
|
|
Can't you use two bracket ends and just weld them to the chassis or use angle iron cut down to make your width and welded in the middle not on
the bends, it's available in different thicknesses and depths.
yours, Pete
I went into the RSPCA office the other day. It was so small you could hardly swing a cat in there.
|
|
James
|
posted on 24/6/04 at 02:33 PM |
|
|
Wingnut,
What about using an appropritately sized piece of box section with one face cut off.
Drill the holes before you cut the face off and you know they'll be parallel too.
Hope that helps,
James
|
|
Viper
|
posted on 24/6/04 at 04:16 PM |
|
|
5mm? how big is this car of yours?
|
|
type 907
|
posted on 24/6/04 at 04:33 PM |
|
|
Quote
"Welds normally fail at the fusion line between the filler and parent metal. "
Mine don't, they can fail anywhere. 
Paul G
Too much is just enough
|
|
Mark Allanson
|
posted on 24/6/04 at 05:33 PM |
|
|
quote: Originally posted by James
Wingnut,
What about using an appropritately sized piece of box section with one face cut off.
Drill the holes before you cut the face off and you know they'll be parallel too.
Hope that helps,
James
Thats what I would do
If you can keep you head, whilst all others around you are losing theirs, you are not fully aware of the situation
|
|
britishtrident
|
posted on 24/6/04 at 06:20 PM |
|
|
5 mm is way too thick even if you are building an truck sized v8 offroader, the greater thickness of material introduces all sort of other pit
falls.
If you must use material of this thicknes use mild steel angle (nb MS -- NOT "bedstead angle" with is a high carbon steel and is not
good for welding)
|
|
Wingnut
|
posted on 25/6/04 at 10:04 AM |
|
|
thanks everyone for the replies, some great ideas there! I feel much wiser now !
In short, I want to raise/lower the pickup points to alter the camber compensation.
Here's a piccie of the pickup. Unfortunately, welding the pickup on the chassis is no longer an option.
I like Blueshifts idea of cutting halfway thru & then welding... sounds like a good compromise.
The car weighs in at about 1100 KG & will run sticky rubber, so I beleive suspension loadings will be quite high. The kit came with the 5mm
brackets & I'm sure they are probably well over engineered.
At present, the pickup-to-chassis bolt and the pickup-to-wishbone bolts are on the same centerline. 'My' pickup will have the two bolts on a
different centerline, maybe 40-50mm apart & so I'd feel happier building a bit more strength into the bracket.
WDYT ?
 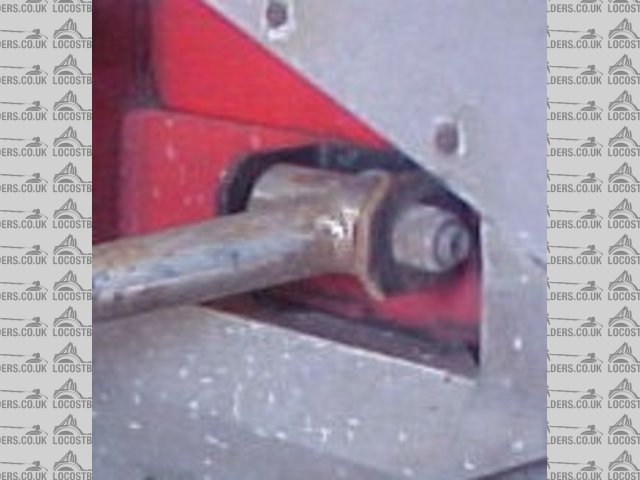 Rescued attachment pickup.JPG
|
|
Bigfoot
|
posted on 25/6/04 at 11:18 AM |
|
|
5mm steel and an appropriate weld takes a hell of a lot of breaking. Trucks weighing several tons have suspension mountings of those proportions. An
1100kg car just does not warrant such things. I have always been of the opinion that we try to make these cars too light, but this is a bit on the
heavy side even for me
We seem to talk about welds breaking quite often, in my many years of engineering, I have never had a weld break, it isn't really supposed to
happen. If you want to build a car, you really have to learn to weld properly.
James suggestion of drilling box section then cutting out one side is probably the easiest if you are not comfortable with steel fabrication, it can
produce a tidy result with little effort.
|
|