alistairolsen
|
posted on 12/9/11 at 02:26 PM |
|
|
Drummond Lathe bearings
I recently acquired a Drummond Round bed lathe which I am in the process of recommissioning. Much like this:
Thanks to Tony at lathes.co.uk for the image
I don’t want to do anything to it which would prevent it from being restored to original, but at the same time don’t intend to do this myself. As such
I have bought a small three phase converter so I can have proper speed control and intend to replace the leather drive belt with a polyvee belt. In
order to fit the new pulley I had to remove the headstock and that led me to scrutinise the bearings.
Before:
My lathe is an early model, with the split headstock bearings which are a little prone to cracking.
Inside these ran the driveshaft, which either from new, or at somepoint later has shrink fit sleeves over it on the bearing surfaces:
Im not sure how best to proceed with it if I’d like a decent level of accuracy, as I see it I could:
1) get the bearings reamed and new sleeves fitted and reinstall it as Drummond intended
2) Fit a spacer to the adjustment screw on the existing bearings and bore them out a little and fit an oilite bush, have new sleeves made and refit
3) Make new bearing housings to hold small needle roller bearings .
I’m not a huge fan of plain bearings unless pressure fed with oil, nor do I like the ‘adjustment’ on these but it may be acceptable. I’m loathe to
modify/damage the existing bearings in case someone wants to do something more faithful in the future, but some have suggested that plain bearings may
be more accurate than rollers (I’m sceptical)
I have a larger lathe I can use to make bearing housings etc and I know a machinist with a crank grinder who could finish the sleeves for me. I’m keen
to end up with a useable machine with decent accuracy for light work Can anyone offer any advice on what they would do for bearings?
Cheers
My Build Thread
|
|
|
Alan B
|
posted on 12/9/11 at 02:54 PM |
|
|
Cool project...just wondering if you'd get a better response in the tools and techniques section though?
Alan
|
|
VanHaydn
|
posted on 12/9/11 at 03:40 PM |
|
|
keep the standard parts
I would keep the standard parts as they are ...put in box for next person if ever to terurn to product original
manufacture new bearing holders and whatever else you need with upgraded rollers and mod the thing with as little work on the original parts
possible...Just retrofit the parts you need to bring it into our century and you got a great little project lathe there....bung a couple of small
stepper motors on it and make it cnc mate...really really cheap and easy to do....
cheers
H
|
|
alistairolsen
|
posted on 12/9/11 at 04:11 PM |
|
|
That was the plan, I dont want to ruin any of the original bits if I can avoid it.
If then, for instance, I carefully store away the bearing housings and the sleeves and then make up new sleeves and have the ground to the right size
and make up new bearing housings on the lathe....
Am I better with plain or roller bearings?
CNC would be an interesting project, but FAR more useful on the big lathe (Hendey 12x30 gearbox lathe) Any how to's/project threads?
Cheers
My Build Thread
|
|
daviep
|
posted on 12/9/11 at 04:47 PM |
|
|
How about going with a taper roller setup, nice and easy to adjust out any lift and would deal with the thrust aspect as well.
After having a better look at the pics anything other than plain bearings is going to be hard to do without raising the centre height, is it possible
to adjust the tailstock if the centre height changes?
What handles thrust at the moment?
“A truly great library contains something in it to offend everyone.”
|
|
alistairolsen
|
posted on 12/9/11 at 04:51 PM |
|
|
The thrust was taken by a shrink ring which ran against the face of one of the bearings.
i looked at taper rollers but as you say, I dont think there is room for the centre.
I measure up and concluded there was enough room for rollers if I got shrink sleeves done and polished in a crank grinder so I didnt need an inner
race. The thrust can be taken with a small roller thrust bearing, I just dont know if after all that id be disappointed and wish id stuck with plain
bearings....
My Build Thread
|
|
oadamo
|
posted on 12/9/11 at 06:27 PM |
|
|
I have one of them chucked down the side of my shed lol. I think the bearing are ok ill have a look.
adam
|
|
chris-g
|
posted on 12/9/11 at 09:42 PM |
|
|
My old round bed Drummond came with an oval shaped rear bearing. It was fitted with an epicyclic back gear built into the pulley. The front bearing
was a special to accommodate the back gear, a machined block with an oil lubed plain bearing. My friend, a CNC machinist, turned and sleeved the rear
of the spindle and then bored and sleeved the original rear bearing. Trouble was that as the two half of the bearing were tightened with the screws it
pinched the shaft. So my friend machined a block and installed a needle roller bearing. I never really got round to setting it up properly as I bought
a Sieg C4.
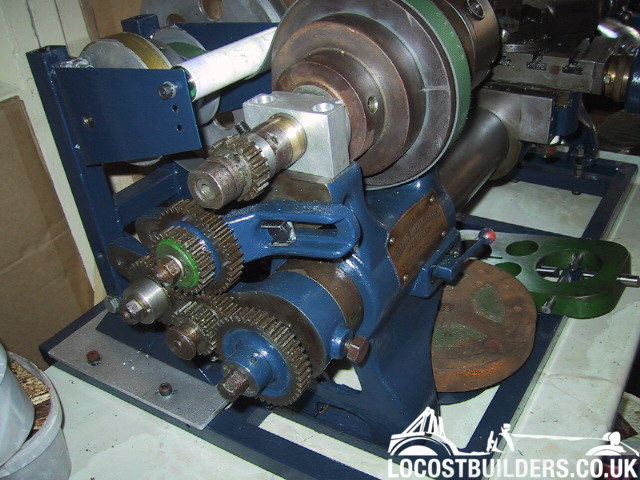
|
|
RAYLEE29
|
posted on 12/9/11 at 10:05 PM |
|
|
Hi, you could bore or ream the bearing housings to clean up then make new journal sleaves.
you can make the sleeves on your other lathe they dont really need to be ground.
thats what i would do if it was mine.
Ray
build diary1
http://picasaweb.google.com/raylee290/RoadsterPics#
build diary2
http://picasaweb.google.com/raylee290/KITCARPICS?authkey=Gv1sRgCI2AouyYgpuQmAE#
|
|
paulf
|
posted on 13/9/11 at 08:25 PM |
|
|
I used to have a Drummond round bed but on mine the bearings were direct in the cast iron headstock.It was ok but tended to seize when used at higher
spindle speeds unless the bearings had oil pumped into them every few minutes.
I would just make some new sleeves for the spindle and bore out the bronze castings to suit, it would be best if the sleeves could be hardened and
ground but turned and polished would work ok.
Taper bearings would need a lot more work to fit and unless got right they are more prone to vibration and can give a poor finish on the work.
Paul
|
|
alistairolsen
|
posted on 15/9/11 at 11:14 AM |
|
|
Chris_g - That looks like what I had in mind, but I dont want to do all the work if Id get a better finish with plain bearings....
Epycylic back gear sounds very interesting, not seen one of those before!
Im still at a loss, the rollers are attractive but I dont want to do the work and be disappointed, specifically if they lead to a poor finish......
My Build Thread
|
|
Dingz
|
posted on 20/9/11 at 12:15 PM |
|
|
Apparently the grey painted ones were often from a naval ship, a friend has one which had a label on with the ships name, I saw one in the submarine
at the museum at Portsmouth.
Phoned the local ramblers club today, but the bloke who answered just
went on and on.
|
|