FuryRebuild
|
posted on 22/4/12 at 09:55 PM |
|
|
seam welding - adding strength for little weight, and pics
So, I remember from years ago, a friend of mine told me how he prepares RS2000 shells – after buying a second-hand one in good shape, it would be
stripped back to the metal and seam welded rather than spot welded.
Mine isn’t seam welded where some of the strong panels join the spaceframe, but stitch welded (i.e. one cm of mig welding for every 5 or 6 cm of
space). It’s quick, stronger than spot welding, but let’s face it – it’s an economy solution.
So, now I want you to queue the Ghostbusters theme in your head and hear me sing “welding makes me feel good”. As a result, I thought I’d quickly try
a couple of quick seams in an easy to weld area to see if it’s worth the hassle. Quick answer is yes.
There are a couple of issues with the quick approach I’ve taken to see if it’s sensible.
- Firstly, grinding the existing the existing powder-coat back isn’t too tough a job (circular belt on the dremmel) but you need to go back quite a
way, which I didn’t. The heat of the weld made the powder-coat peel back. I’m going to get a blow-torch and see if this will get more of the
powder-coat off. This leads me to my next point:
- The powder-coat gives off fumes when burning away. I’ve had a sniff of this and it’s not pleasant. I will need to do the burning off with the
garage door open, ideally with a breeze. Once I’ve burnt off the bits I want off, I’ll then weld it. One big burning. Maybe with a fan.
- There is a little inevitable powder-coat down between the gap of the panel and cross-member it’s stitch-welded to. This will cause a little
pollution of the weld. I have a really nasty pointy grinding tool for the dremmel which gets most of the powder coat out. It’s evil, and I’d love to
turn it on a dentist some time.
So, here’s the welds – they look good and really nicely round the corner off. The holes aren’t blow-throughs but screw-holes from whatever was mounted
on there.
Firstly is a close-up of the seam.
 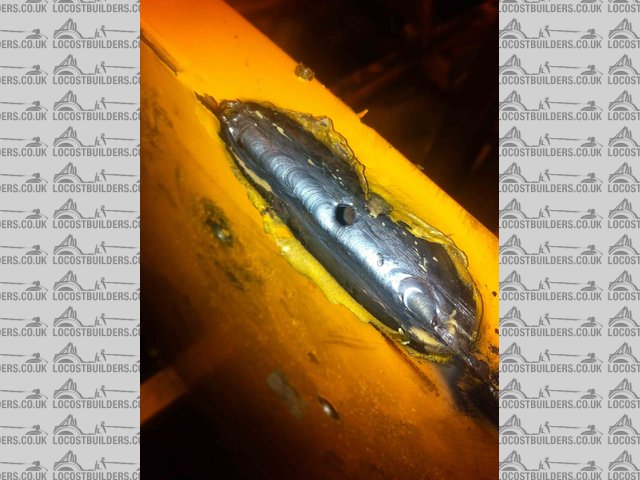 Description
Secondly, here are a couple of seams, running into the stirch-weld between them
 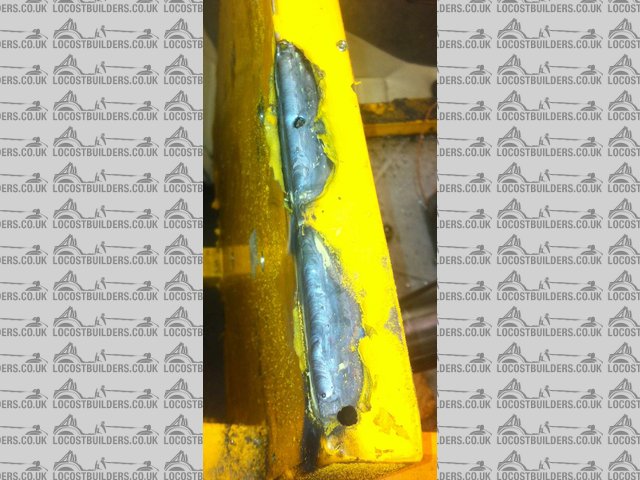 Description
When all you have is a hammer, everything around you is a nail.
www.furyrebuild.co.uk
|
|
|
snapper
|
posted on 23/4/12 at 08:40 AM |
|
|
The seam welding on an RS2000 was to prevent it falling apart on stage rally's, if a full roll cage was fitted that provided most of the
rigidity
On a Fury which has a square tube chassis the stitch WD you have has proved to be quite sufficient.
Beware of the powder coat, wear a mask you know it makes sense
I eat to survive
I drink to forget
I breath to pi55 my ex wife off (and now my ex partner)
|
|
iank
|
posted on 23/4/12 at 08:52 AM |
|
|
Flap disc in an angle grinder (used gently!) is the best method I've found for removing powdercoat.
Something like this
http://www.screwfix.com/p/bosch-flap-discs-115mm-80-grit/32902
Still wear a mask as it turns it back into powder but better than fumes.
--
Never argue with an idiot. They drag you down to their level, then beat you with experience.
Anonymous
|
|
FuryRebuild
|
posted on 23/4/12 at 08:53 AM |
|
|
Hi Snapper - your opinion is always valued.
Do you think:
1) not worth it - no noticable gains
2) you do get gains in strength, but a lot of effort
3) another opinion
And yes - molten plastic smells horrendous. I'll look for the right filter mask if I'm going to be burning the coat away.
When all you have is a hammer, everything around you is a nail.
www.furyrebuild.co.uk
|
|
Liam
|
posted on 24/4/12 at 04:08 PM |
|
|
Personally I can't see it contributing anything noticable in terms of strength. It's different with a monocoque production car as the
spot-welded panels are all there is and the factory spot welding can be minimal to say the least. With a locost type chassis the strength is already
there in the fully welded spaceframe and the panels aren't doing a massive amount for strength or rigidity. They contribute for sure, but stitch
welding is more than adequate to keep them in place - I've never heard of a welded panel falling out of a locost so they're not a weak
point. I doubt you'll see any gain in strength and rigidity by seaming them up, imho. More likely to risk distorting the chassis with the heat
and leaving it under stress.
But hey if you want to do it and think it looks good then why ever not 
|
|
MikeRJ
|
posted on 24/4/12 at 04:48 PM |
|
|
Full seam welding is quite likely to introduce some distortion. Personally I'd stick with stitch welding it. FWIW many "seam
welded" rally cars are actually stitch welded for this reason.
|
|