Avoneer
|
posted on 11/3/05 at 11:50 PM |
|
|
Shaping angles easily
Would the belt sander bit of this bench grinder be any good for the angles on the chassis bars?
60, 80 or 120 grit available?
Pat...
No trees were killed in the sending of this message.
However a large number of electrons were terribly inconvenienced.
|
|
|
Avoneer
|
posted on 11/3/05 at 11:50 PM |
|
|
Oops, forgot the pic:
 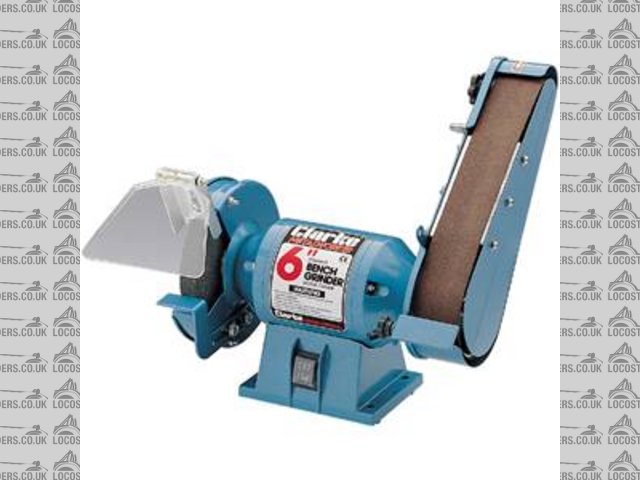 Rescued attachment MM060713050C.jpg
No trees were killed in the sending of this message.
However a large number of electrons were terribly inconvenienced.
|
|
chunkielad
|
posted on 11/3/05 at 11:55 PM |
|
|
Would't a chopsaw be cheaper/better?
|
|
Avoneer
|
posted on 11/3/05 at 11:58 PM |
|
|
I need a new grinder anyway and only ever used one wheel.
The main question is will the belt do the job?
Pat...
No trees were killed in the sending of this message.
However a large number of electrons were terribly inconvenienced.
|
|
Avoneer
|
posted on 12/3/05 at 12:12 AM |
|
|
And it would be mainly for the shallower angles.
Pat...
No trees were killed in the sending of this message.
However a large number of electrons were terribly inconvenienced.
|
|
Alan_Thomas
|
posted on 12/3/05 at 12:16 AM |
|
|
Not really the right tool for getting the angles right. You want to get the angle right when you make the cut. If you get the angle slightly wrong a
good 'bastard' file will remove metal as quick as the belt and less dangerous too.
'Sanding' it away afterwards will be time consuming and you will always be fitting a new belt. If you have money burning in your pocket a
much more versitile tool than a static belt sander is a 'power file'. this is a thin abrasive belt which is fantastic at cleaning up welds
where they show and removing the graining from alloy sand castingds proir to polishing
|
|
MkIndy7
|
posted on 12/3/05 at 12:38 AM |
|
|
Or you could make some kind of Jig that would feed the rail in at the correct angle into the face of a grinding disk
(either a captive angle grinder or bench grinder), like a mitre to get the correct angle and a nice neat face.
Or buy a bench grinder and make or buy something like this
http://www.machinemart.co.uk/product.asp?p=060221110&r=2040&g=106
|
|
chunkielad
|
posted on 12/3/05 at 12:59 AM |
|
|
Surely chopsawing it right in the first place would be the best option.
|
|
dmottaway
|
posted on 12/3/05 at 01:51 AM |
|
|
I used a chopsaw to cut the angle, but with the tube a bit long, then tried to dress it down with a belt sander with 80 grit. Pretty quickly ruined
the whole thing. LA & LB quickly became H tubes.
dave
|
|
kb58
|
posted on 12/3/05 at 01:56 AM |
|
|
Get one of those cheap horizontal/vertical bandsaw. Using the belt sander will take forever, throw grit all over the place, and you'll be going
through belts like crazy.
Mid-engine Locost - http://www.midlana.com
And the book - http://www.lulu.com/shop/kurt-bilinski/midlana/paperback/product-21330662.html
Kimini - a tube-frame, carbon shell, Honda Prelude VTEC mid-engine Mini: http://www.kimini.com
And its book -
http://www.lulu.com/shop/kurt-bilinski/kimini-how-to-design-and-build-a-mid-engine-sports-car-from-scratch/paperback/product-4858803.html
|
|
phil m
|
posted on 12/3/05 at 08:56 AM |
|
|
made mine using this ---grinder and a £24 stand
phil
 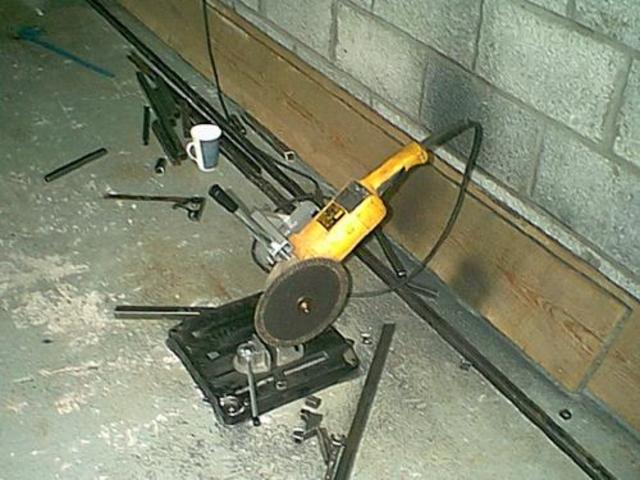 Rescued attachment image241.jpg
|
|
britishtrident
|
posted on 12/3/05 at 08:58 AM |
|
|
The correct term is a "Linisher" and it isn't really suitable as the sharp edges will tear the belts.
Just cut accurately with hack saw and trim with a file or careful use of a flap wheel sanding disc in the angle grinder
|
|
Avoneer
|
posted on 12/3/05 at 09:14 AM |
|
|
Thanks guys.
I have cut most of my steel with my hacksaw and I get a vertical cut so no problems there.
Just wondered how to get the little anlgles easily. Will use the file route.
Thanks guys.
Pat...
No trees were killed in the sending of this message.
However a large number of electrons were terribly inconvenienced.
|
|
Volvorsport
|
posted on 12/3/05 at 11:06 AM |
|
|
chop saw , with 2 inch depth cut - £68 +VAT - wont use it all the time , so its now mine .
www.dbsmotorsport.co.uk
getting dirty under a bus
|
|
RogerM
|
posted on 12/3/05 at 11:11 AM |
|
|
Well I fell I must counter argue most of what is said here!!!
I am using a chop saw to get the angles but leaving a bitr extra and using a Clarke bench belt sander (60 grit belt) to bring it back to the correct
length.
There are also several places on my chassis where I have to drop sections out of tubes as the slot together. For these I am either using a
'plasma' (i.e. 1mm thick) cutting disc in a grinder or a band saw to get the shape and then using the belt sander to square up the edges.
I must admit that I am deburring the edges first before dropping the tube on the belt.
I am having no problems with this at all, the same disc and belt have been on the machine since before Xmas and at the rate they are wearing they
might still be there next Xmas.
However I must state that I am using a belt sander not a linisher.
A belt sander can be used for shaping and cleaning up all sorts of things through the build so I would recomend one to anybody.
Just an alternative point of view.
|
|
clbarclay
|
posted on 12/3/05 at 11:53 AM |
|
|
If you mark the angle on the metal first, the grinding stone part of the grinder works pritty good.
Jigs are fine untill the grinding stone/disc starts to wear unevenaly. A steady hand (doesn't need to be too steady) and a line to work to is
all you need.
Not having a sanding belt on your grinder also means that you can have 2 different stones, useually 1 fine and 1 course.
|
|
WIMMERA
|
posted on 13/3/05 at 12:08 AM |
|
|
It's been my experience that a belt grinder will remove metal at around 3 times the speed of a grinding wheel. The most used and abused tool in
my shop is a belt grinder very similar to the one pictured, wouldn't be without it.
Wimmera
|
|
Cita
|
posted on 13/3/05 at 08:24 AM |
|
|
It seems that those who have tried it are all in favor (except dmottaway) and those who dont have the tool are against it
  
|
|
clbarclay
|
posted on 13/3/05 at 08:33 AM |
|
|
Rahter than using a belt sander I have a large foam wheel with a sanding beltaround it, works v.well on wood, but not metal.
|
|
WIMMERA
|
posted on 13/3/05 at 09:22 AM |
|
|
I thought dmottaway gave it a great plug he said it happened quickly.
Wimmera
|
|
Jonr
|
posted on 13/3/05 at 12:58 PM |
|
|
quote: Originally posted by phil m
made mine using this ---grinder and a £24 stand
phil
Sorry to put down your toolmaking skills, but I would spend the extra quid and get one with a guard. Grinding discs are scarey things when they
explode!! Also looks like you have taken a chop saw cut off disc (flat centre)and mounted it on a 9" grinder?? If thats the case compare the
rpm rating of the disc and grinder. Grinder runs at about 7000rpm, chop off saws at about 3000 rpm. So your running the blade twice as fast as
it's desgned for, twice as likely to explode!
Thought the pictures might illustrate the point, these aren't too gruesome, but there are some pretty gruesome grinder FATALITY pictures around.
(Disc impacting the head rather than the arm)
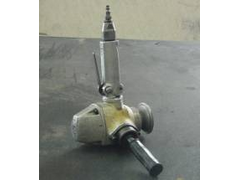 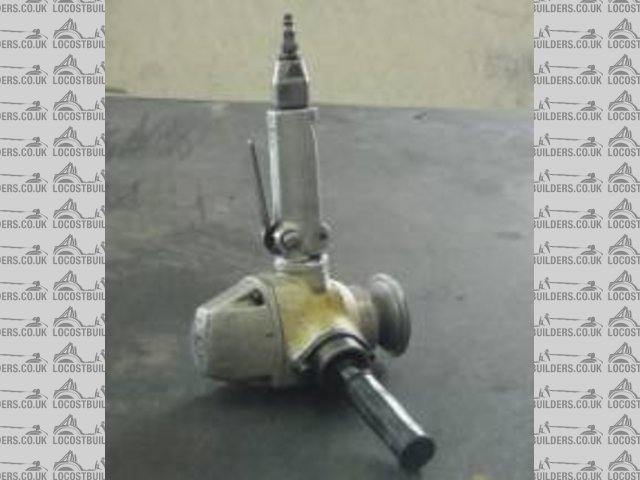 air grinder
 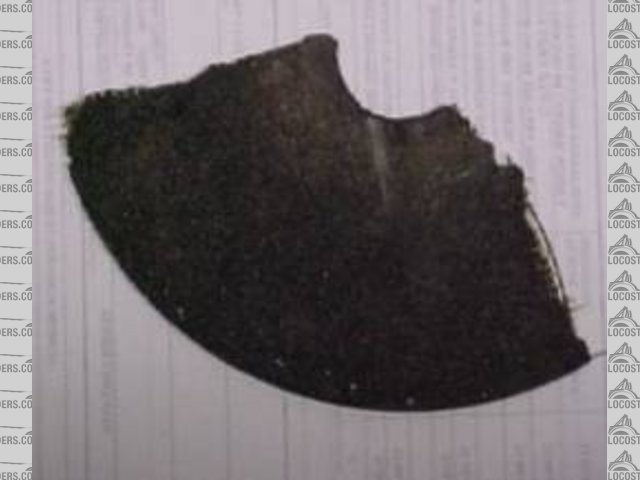 grinder blade
 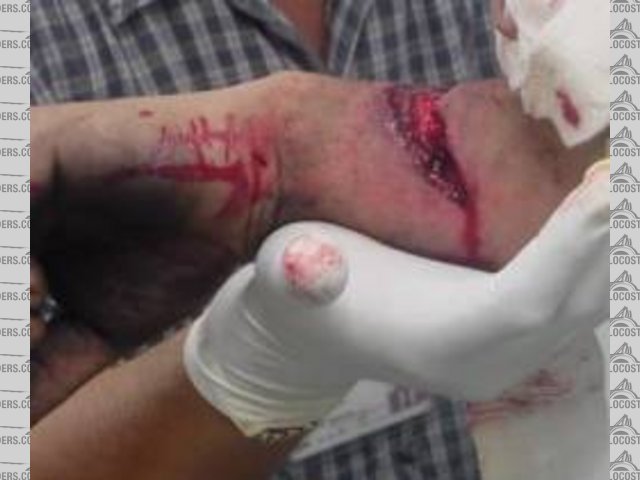 blade injury
Please don't take this personally Phil, just couldn't live with myself if I didn't comment and try to keep you with all the body parts
you need to enjoy the car.
|
|
the JoKeR
|
posted on 13/3/05 at 02:12 PM |
|
|
That last picture put my off my breakfast. I use safety as a good excuse to add to the tool collection. Since my wife doesn't know how the
tools work or what they're for, I'm pretty much able to buy whatever I want!
I use a pair of belt sanders:
and
depending on the size of the material being worked on. The smaller 1" belt sander is for small pieces, while the 4" belt works well for
dressing large pieces. The larger one could be used as originally asked, for making the actual angles, but it's not very precise unless a jig
would be holding the metal in place. As others have stated, but best bet considering how many cuts there are in a typical build would be to purchase
a chop-saw or a band-saw to make the cuts.
A chop-saw is fast, noisy, and makes a somewhat rough cut which needs clean up prior to using the cut stock. The band-saw is slower, but often pretty
quiet and leaves you with a much cleaner cut which only needs minimal prepping prior to using the cut piece. Either way, a grinder with a flap disk
would go along with either one to do the final prep work on the stock to make it ready for use. Angle grinders can often be found nice and cheap, so
I keep three of them set up with different disks - one with a small cut-off wheel, one with a grinding wheel, and one with the sanding flap-disk.
Yes, the tools add up in cost, but they off-set the hospital bills from using the wrong tool for the job! Consider how much time you'll save by
using the tools and how much your time is worth. If you have no use for the tools after the project is done, sell them to to other builders to regain
part of your original investment.
Yes, I have a chop saw AND a band saw, too.
__________________________
Jeff
http://www.midwestwelding.com
http://www.locostusa.com/forums/
|
|
clbarclay
|
posted on 13/3/05 at 05:01 PM |
|
|
quote: Originally posted by WIMMERA
I thought dmottaway gave it a great plug he said it happened quickly.
Wimmera
A revolving block of foam with grit round the edge is probably not the same as a belt. Speed and grit grade is probably also different.
As for exploding grinding/cutting discs, how many people here know what the code on a disc means?
Not only do the help with safety, they can also make a big difference to disc performance.
The right tool for the job.
Band saws a good, but power hack saws with a fore/arft movement are tricky peices of kit to set up, particuarly if you want them to cut square.
[Edited on 13/3/05 by clbarclay]
|
|
clbarclay
|
posted on 13/3/05 at 05:04 PM |
|
|
Another advantage of a disc is that you can grind fishmouths on round tube a lot easier. Sanders don't dress to get a good edge back after
you've only been using the edge of the belt.
[Edited on 14/3/05 by clbarclay]
|
|
NS Dev
|
posted on 14/3/05 at 04:25 PM |
|
|
Belt sander (linisher) is a brilliant piece of kit, I have one like the upper of the two pictures above, though i usually use in in the flat position,
and for deburring and sanding accurate angles it is brilliant.
As an interesting point, I agree fully that it seems to remove metal much faster than a disc/wheel, and also industrial tube fishmouthing machines
(the older ones) often use a linishing belt over a pair of rollers, one of which is sized to give the correct fishmouth.
It will work fine for the tubes used in a locost, you can use various grit belts to get the finish you want anf I haven't broken one yet.
Also.......it is about the only way I can get a dead square cut end on thin 2.5" exhaust tubing! (the bandsaw or hacksaw both wobble very badly
on this stuff and you can't clamp it tight as it will collapse)
I would junk the bench grinder altogether unless you use it with a green wheel for sharpening carbide lathe tools, and just get the linisher in the
upper of the two pictures above, it will basically do anything the grinder will do, as well as being a lot easier and more controllable.
|
|