jkarran
|
posted on 26/1/08 at 06:42 PM |
|
|
TIG porosity problems - steel
I've not used the TIG much on steel so it could just be me... I'm getting loads of bubbles in my weld, it looks like a metal crunchie, I
don't remember it being like this before and I have some nice sound welds on the kitcar done (by me) with this welder/gas.
I assumed it was a cleanliness issue so I reground the tungsten, paid extra attention to cleaning back to bare metal with a file/paper... still it
bubbles.
Maybe the rods? They're old so I clean them with emery paper and a cloth before use... but it bubbles when I'm not using filler.
I don't think the current is too high, it takes 2 or 3 sec to form a puddle. I'm not using any downslope but it bubbles before I shut
off.
Gas is Argon, 10L/min. Post-gas 2 or 3 sec but it bubbles before I shut off.
I've tried it on a few different bits of stock so it's not crap steel.
Tungsten is the 'red' one which my instructions say is for steel.
Settings:
DC
Current ~65A
No up-slope
No down-slope
No pulse
Post gas ~3sec
Tungsten ~2.5mm, ground to a point
Though it bubbled last week when using the pedal to get a nice up slope, small puddle and downslope.
Annoying!
Any ideas? Sorry for the windy post, it's driving me up the wall.
jk
[Edited on 26/1/08 by jkarran]
[Edited on 26/1/08 by jkarran]
|
|
|
nitram38
|
posted on 26/1/08 at 07:05 PM |
|
|
Make sure your tungsten is too a point and not rounded like when you weld aluminium. Also it should stick out a little further than when you do Ali,
perhaps about 7-10mm.
Make sure that you have post gas flow after you stop welding and keep the torch over the weld until it cools.
Pulling the torch away too quickly can allow oxygen into the molten pool.
[Edited on 26/1/2008 by nitram38]
|
|
short track 123
|
posted on 26/1/08 at 08:42 PM |
|
|
What sort of argon are you using you can get this sort of problem if your are using the wrong argon.
Your flow rate sounds a bit high as well
5-8 L/min on carbon steels all depends on what type of joint and thickness of the metal.
In general the thicker the metal more flow and bigger electrode and filler rods.
Hope you get it sorted
Regards Jason
|
NOTE:This user is registered as a LocostBuilders trader and may offer commercial services to other users
|
clanger
|
posted on 26/1/08 at 09:08 PM |
|
|
Try cleaning joint with wire brush only.
You may be introducing impurities from the file or emery.
Just a thought.
|
|
IDONTBELEIVEIT
|
posted on 26/1/08 at 09:24 PM |
|
|
cold start and 1.5 seconds of up-slope to preheat parent metal,1 second of pre-weld gas,couple of seconds of down slope,3-5 seconds of post
gas,pureshield argon,not co2 argonmix,tep red thoriated tungsten is the one for DC welding,though not much difference in the zirconiated only 5% just
for coded welds,the length if you like of the sharpened tungsten should be 1 1/2 times the diameter2.4mms are for 130 amps and above as a genereal
rule youll need a 1.6 mm tungsten and between 35 and 50 amps (depends how fast you can weld)and yes nice clean metal,is it cr4 (shiny)mild steel your
using or hot rolled (dull and scaly)hope this helps wayno
 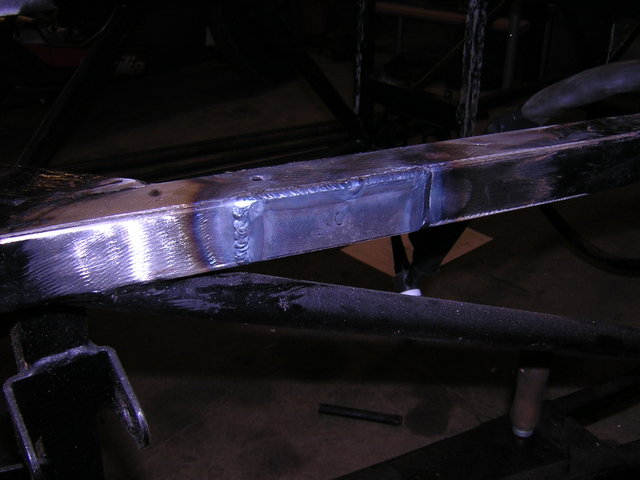 Rescued attachment DSCN1557.JPG
|
|
caber
|
posted on 26/1/08 at 09:28 PM |
|
|
Must be contamination from somewhere steel must be absolutely cleanfor an area aroound he weld I usually have a 6m margin around he weld.Rods also
have to be pristine and meant for TIG gas rods don't do. Sometimes the base metal can have contamination in it if it was rusty you can still
leave rust there that you can't see unless you take a good depth off the metal when cleaning.
Good luck
Caber 
|
|
madteg
|
posted on 26/1/08 at 09:47 PM |
|
|
Are you shaw that you are using argon pureshield as it looks like you are using gas ment for a mig set.
|
|
JohnN
|
posted on 26/1/08 at 10:20 PM |
|
|
IT'S THE RODS !!!!!!!
The problem you have, I' sure, is related to the filler rods you are using. Rods for Oxy-acetylene use, ie general filler rods, basically are no
good. If you are using some old rods, chances are they are not pure enough steel.
I had exactly the same problem, it was solved by getting some mild steel filler rods certified for TIG use
[Edited on 26/1/08 by JohnN]
|
|
John Bonnett
|
posted on 27/1/08 at 01:22 PM |
|
|
quote: IT'S THE RODS !!!!!!!
JohnN is absolutely right.
For TIG welding mild steel gas rods are of no use. You need triple deoxidised rods Once you are using these, your troubles will be over.
John
|
|
Doug68
|
posted on 27/1/08 at 02:21 PM |
|
|
It could well be the rods, but also...
I get this issue when the Tungsten is poking out to far. As a rule it shouldn't be more the 1/2 the diameter of the cup, but you can get away
with more in some situations I've found.
Doug. 1TG
Sports Car Builders WA
|
|
jkarran
|
posted on 28/1/08 at 09:38 AM |
|
|
Thanks for all the tips guys.
Argon is pure, not CO2 mix, from Air Products. I mostly use the set for Aliuminium on which it works fine. Flow isn't adjustable, there's
an inline orifice comes withthe bottle so it may be a little high.
Rods were bought from a welding suppliers for TIG use but are looking a little sorry for themselves. The bubbling happens with or without filler
though it's worse with. I'll buy some more anyway.
Could be my wire brush, I'll buy a 'clean' one.
Tungsten is ~2.5mm sticking ~7mm out of ~12mm cup. Tip is ground to a point, grinding maks run up/down rather than around. It is blueing more than it
used to... I wonder if the gas is low on flow as the pressure is going down (bottle shows half full).
Have tried various different steels, hotrolled mild with mill scale filed off, galvanised mild (with zinc ground off a long way back from the joint),
painted mild with paint sanded off.
Thanks again, I'll let you all know how I get on,
jk
|
|
John Bonnett
|
posted on 28/1/08 at 06:10 PM |
|
|
quote: It is blueing more than it used to
The tip should not blue at all. If you have sufficient argon flow (6 l/hr) do you have enough post gas. I have set mine to 7 seconds and I get no
blueing at all. Also, try to keep the filler in the gas shield all the time.
Please keep us posted.
atb
John
|
|
907
|
posted on 28/1/08 at 08:23 PM |
|
|
Hi,
All the advise on this thread is spot on, so I will just mention one or two other things.
First I would check for argon leaks. You may have 10 l/min at the reg but do you have that at the torch?
Check your line for damage from weld spatter or grinding sparks. Check the gas solenoid inside the plant and the gas connection in the torch.
I would also advise on the use of a flow meter (see pic below, eBay item no 310012967522, NTDWM), as they are spot on, unlike most regulators.
If you haven't got a 3/8"bsp outlet then fit it in line. £14 well spent IMHO.
A technique problem? Maybe.
I will assume that you are not holding an excessive arc gap or tilting the torch back more than you should, but you could be puddling the pool for too
long. Start the arc, get some filler in there, and get going. The less time the metal is molten the less time for contamination.
Mild steel is not the purest of metals and it is normal to experience problems if everything is not as it should be.
Hang around and it soon "boils", if I may use an nontechnical term.
One thing to remember is that even if all is well on top, the underside, if welding thin sheet with full penetration, is free to adsorb whatever
oxygen it likes which then mixes throughout the weld.
I'll get shot down in flames for saying this but personally I back with argon whenever practical.
As a matter of interest do you get the same problem with fillets? Normally you tend to get better gas coverage in a 90deg fillet weld.
HTH
Paul G
 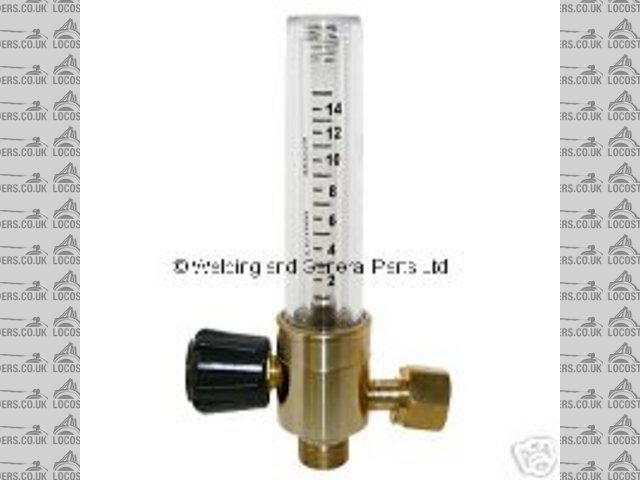 Rescued attachment argon flow meter.jpg
|
|
Doug68
|
posted on 29/1/08 at 09:02 AM |
|
|
One more silly suggestion, you say you are mostly setup for Ali?
You did switch to a +Ve earth and DC for doing steel.
BTW I can't go a day without forgetting to attach the earth before attempting to arc up.
Doug. 1TG
Sports Car Builders WA
|
|
jkarran
|
posted on 29/1/08 at 09:56 AM |
|
|
Thanks guys for all the good suggestions.
The leak idea was a good one, I found a leak a week or two back and fixed it.
Anyway, problem sloved... turns out it was a problem with the shield gas but nothing as technical as I'd feared. I recently moved the welder to
a friend's place to do some work for him.
At home it sits on my left - fine.
At my friend's place it sits on my right - crap porus welds
Turns out the cooling fan was causing enough of a draught to blow away my shield. Prop up an old Haynes manual on the bench and hey presto... spot on
clean welds
About as good as it gets with my very limited skill:
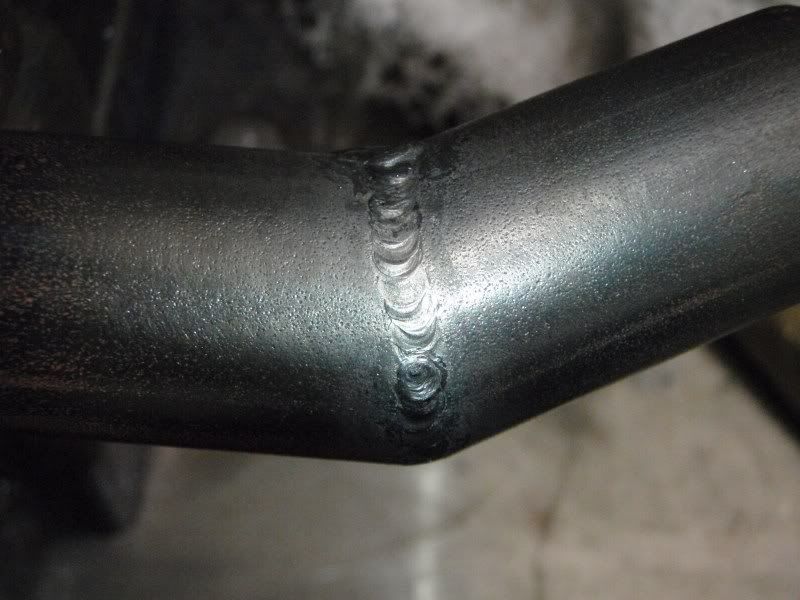
|
|
NS Dev
|
posted on 30/1/08 at 07:29 PM |
|
|
one to watch for here is steel, as 907 said.
I have had some crap steel boil up no matter what I did with it.
Also, watch if you are welding plasma cut edges, always grind the hardened plasma edge off first, that will boil up like buggery if you try and weld
it as-is.
Retro RWD is the way forward...........automotive fabrication, car restoration, sheetmetal work, engine conversion
retro car restoration and tuning
|
|